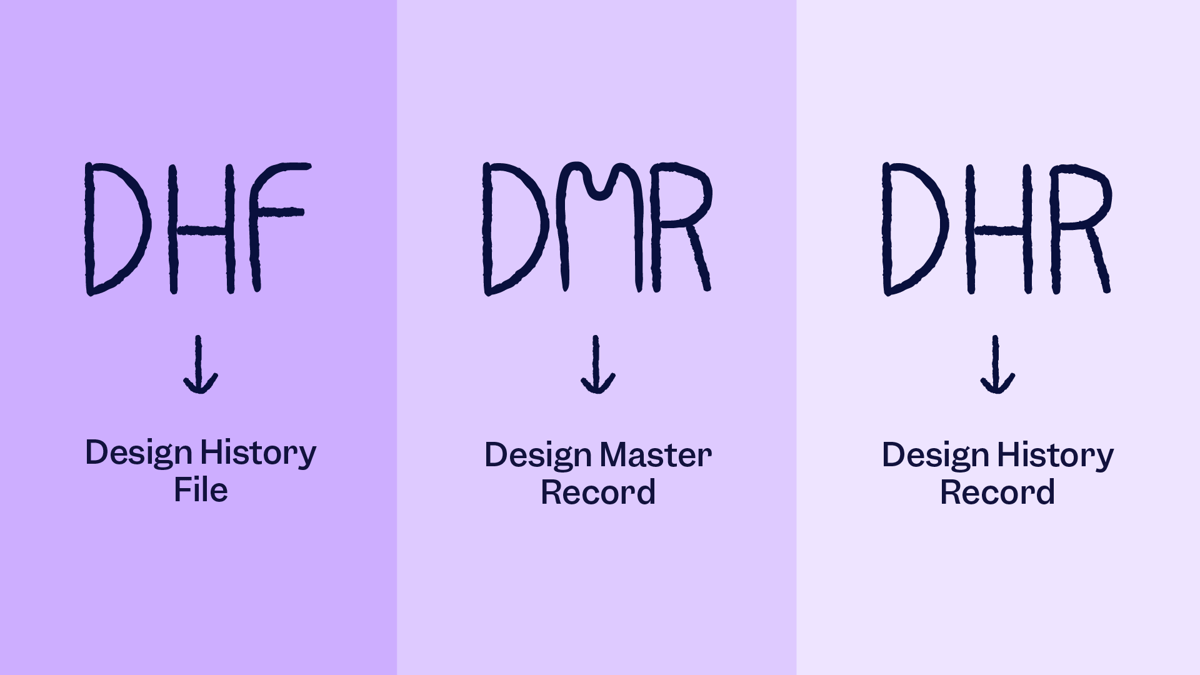
In the medical device industry, there are tons of abbreviations. And as a medical device professional in the US working with Quality Management Systems Regulations (QMSR), or 21 CFR Part 820 as it’s technically known, you can easily get lost in this acronym ocean!
Until recently, the most important (and most confusing) abbreviations to understand were: DHF, DMR, DHR. These three abbreviations have been commonly used by the FDA for decades in relation to record-keeping requirements for medical device quality regulation:
- DHF - Design History File
- DMR - Device Master Record
- DHR - Device History Record
Although these traditional terms have been around for years, they are becoming ‘defunct’ in 2026 as the FDA has published new rules for the quality management of medical devices. Until then, the DHF, DMR, and DHR for medical devices still need to be managed compliantly.
This post explains the DHF, DMR, DHR, and explains how the regulations are changing, and what that means for your company.
Don’t miss our QARA guide to medical device quality management systems to understand the bigger picture of quality management in this changing landscape.
DHF, DMR, DHR, QMSR, and other important definitions
In the context of QMSR, or 21 CFR Part 820, the quality management regulations for medical devices in the US are three different files: DHF, DMR, DHR.
Although they sound similar, they are quite different and contain different documents generated in different steps of the medical device design and manufacturing process. These terms refer to the required documents that medical device manufacturers must create and make available for auditors to show the compliance of the medical device to achieve FDA approval - and therefore access to the US market.
DHF - Design History File
The Design History File (DHF) documents how a medical device was designed and tested to meet end users’ needs. The DHF must contain or refer to the documentation of design reviews, validation, controlled design, and approved design inputs and outputs.
Until February 2026, when the new rules come into effect, 21 CFR 820.30, states that “each manufacturer shall establish and maintain a DHF for each type of device.”
DMR - Device Master Record
The Device Master Record (DMR) can be considered an instruction manual for the compliant manufacturing of the medical device. A DMR had to contain or refer to the information that was required to build the device, including specifications, acceptance criteria, drawings, BOMs (Bill of Materials), and maintenance/servicing procedures.
Currently, the FDA mandates DMRs for each type of medical device according to 21 CFR 820.181, and these requirements will continue until February 2026.
DHR - Device History Record
The Device History Record (DHR) contains all documents to prove that the instruction manual has been followed while manufacturing the medical device. A DHR refers to the date of manufacturing, quantity, acceptance records of manufactured medical devices, and unique device identifiers (UDIs) or any other unique device labels.
Currently, the FDA mandates that each manufacturer shall establish DHRs for each batch, lot, or unit produced based on 21 CFR 820.184.
International Quality Management System (QMS) for medical devices ISO 13485:2016
ISO 13485:2016 is an international standard that specifies requirements for a QMS for medical devices. The FDA wanted to align their requirements for medical devices with these standards, which is the reason for the recent regulatory changes to 21 CFR Part 820.
The ISO 13485:2016 refers to a Design and Development File (DDF) and a Medical Device File (MDF), which must be kept, which contain records similar to those housed in the DHF, DHR and DMR.
QSR and QMSR
21 CFR Part 820 used to be called Quality Systems Regulations (QSR) until New Year’s Eve 2024, when the FDA announced changes to the regulations and gave them a new name: Quality Management Systems Regulations (QMSR).
The new QMSR is much more aligned with international standards, ISO 13485:2016, and doesn’t mention the DHF, DHR, DMR files at all. But that doesn’t mean the requirements are vastly different. Even though QMSR doesn’t refer to the DHF, DMR, DHR files, the record-keeping requirements aren’t actually changing a great deal.
The difference between DHF, DMR, and DHR
Until 2026, you still need to know what DHF, DHR and DMR for medical devices stand for and how to stay compliant. Even though these abbreviations sound very similar and confusing at first, here is a quick trick so you will never confuse them again:
Scilife Tip:
Focus on the last letter. The “R” stands for “record” and means that the abbreviation must be related to the “device” and not the “design.” This will automatically tell you what the first letter “D” stands for.
In this way, you will easily be able to tell the difference between DHF, DMR, and DHR for medical devices!
- The Design History File recounts the history of the design and ensures that it is designed according to FDA regulations.
- The Device Master Record focuses on manufacturing the device and ensures that all required activities are included to build, test, package, and service it.
- The Device History Record compiles the documents that are used to manufacture the medical device.
The process begins with the history of the design (the DHF) and continues to record how the device (the DMR) was manufactured and tested. Then it continues with the history of the device (the DHR) that contains all info on how the device is built.
Here’s the documentation that DHF, DMR, and DHR for medical devices include:
Design History File (DHF)
- Design and development plans
- User needs
- Product requirements
- Design inputs
- Design outputs
- Design review records
- V&V (Verification and Validation) protocols and requirements
- Design verification results
- Change control and CAPA records
- Risk management plan and report
- Design transfer materials
Device Master Record (DMR)
- Design specifications, such as drawings, composition, formulation, component specs, and software specs
- BOMs (Bill of Materials)
- Production processes
- Equipment specifications
- Packaging and labeling specifications
- Quality assurance procedures and specifications
- Installation, maintenance, and servicing procedures
- Acceptance criteria
Device History Record (DHR)
- Acceptance records demonstrating compliance with the DMR
- Product and component IDs
- Material lots and serial number
- Production records
- Non-conformance reports
- Date(s) of manufacture
- Quantity manufactured
- Quantity released
- Primary identification labeling for each unit
- Unique device identifier (UDI) or universal product code (UPC), plus any other device identification(s) and control number(s)
The difference between DHF and DDF
In the development stage, the Design History File (DHF) needs to enable auditors to evaluate the compliance and consistency of the design controls. This documentation should contain all evidence, documents, and records to meet the requirements in terms of design and development – including any changes made to the medical device. In the EU, the Design and Development File (DDF) houses similar records, as defined in ISO 13485:2016.
The difference between DMR and MDF
The Device Master Record (DMR) describes the stage of transferring the design to the manufacturing of the medical device. At this stage, you need to combine all relevant manufacturing records to generate the DMR. In the US, the old version of FDA 21 CFR 820.181 defines a DMR as a required set of records that contains all parts, specifications, and designs necessary to build a medical device.
In the EU, ISO 13485:2016 demands a similar Medical Device File (MDF), which can be thought of as the European equivalent to the DMR.
Quality Management System Regulation (QMSR) update: What's happening to the DMR, DHF, DHR?
On New Year's Eve 2024, the FDA issued a final rule that 21 CFR Part 820 was changing, along with its name, from Quality System Regulation (QSR) to Quality Management System Regulation (QMSR).
They’re making these changes so that quality management regulations for medical devices in the United States are better aligned with the international standard ISO 13485:2016, which doesn’t mention DHF, DMR, DHR files. The effective date that QMSR comes into force is February 2nd, 2026.
The FDA’s new Medical Device File (MDF)
The QMSR is moving away from the traditional terms: DHF, DHR, DMR, which were used in the previous QSR regulation.
Instead, it’s adopting the term “Medical Device File” (MDF), in line with the international standard ISO 13485:2016. From 2016, the MDF will include all of the documents necessary to show that a device conforms to QMSR requirements, including design and development, production, and production activities since going on the market.
The good news is that most of the record-keeping requirements for medical devices aren’t changing in any major way. Much of what was contained in the DHF, DMR, and DHR for medical devices will still need to be documented.
Scilife Tip:
Just because the changes to record-keeping requirements aren’t major doesn’t mean that medical device companies can waste time getting up to speed. You must prepare their QMS and devices now, or risk noncompliance with QMSR.
But don’t panic! The FDA consistently points out that the requirements for QMSR are really very similar to the international requirements for ISO 13485:2016, which any medical device company that is operating internationally would already be following.
In fact, the FDA expects that by aligning 21 CFR Part 820 with ISO 13485:2016, a lot of “redundant effort” that some manufacturers make in complying with both US and international standards will be saved. Which can only be a good thing!
Managing DHF, DMR, DHR: Best practices for quality management record-keeping for medical devices
Even though the DHF, DMR, DHR are terms that are becoming defunct in 2026 and are being replaced by a single file, the MDF, record-keeping best practices for the quality management of medical devices will remain similar.
Here are some best practices to follow:
- Establish a robust QMS
Generally, you should ensure that your QMS provides a robust framework for managing all aspects of the medical device lifecycle, from design through to approval and quality control. Using a digital QMS can improve traceability and automate workflows, helping to ensure compliance and increase efficiency.
-
- Centralized system: Create a centralized repository to help organize documents, including different versions (draft, review, or approved) and ensure proper version control and accessibility control
- Robust document control procedures: Outline how documents are created, reviewed, and approved
- Secure access controls: It’s not necessary for everyone to have access to all files. You need to define who can access, edit, and approve documents depending on their roles and responsibilities
- Formal change management: Implement a formal change management process so that any changes to the design, manufacture, testing, or record-keeping procedures can be properly managed
- Educate personnel: Personnel should receive ongoing, documented training related to their specific roles and responsibilities in relation to QMSR record-keeping, at all stages of the medical device life cycle
- Conduct regular audits: Don’t get caught off guard by the FDA! Conduct your own internal audits to ensure compliance with QMSR record-keeping requirements.
-
During device design stages (currently relevant to managing a DHF)
When developing medical devices, first comes the design stage. Records should be kept that keep together all the information on how the device was first designed, improved, and perfected.
-
- Start early: This ensures completeness of records and compliance
- Rigorous record keeping: Document every decision, activity, or approval related to the design and development of the device
- Prioritize traceability: Well-maintained records of the device design stage show clear traceability from user needs to design inputs and outputs
- Support continuous improvement: Devices are often improved, and the design files should make it as easy as possible for improvements and inform any future efforts
-
Standardizing production instructions (currently relevant to the DMR)
You’ve perfected the medical device design, and now you need to record the “recipe” so that each time a device is made, it’s produced consistently, according to design specifications.
-
- Record all production instructions and specifications: Records should contain all relevant manufacturing information
- Version control: All documents should have clear version numbers, dates, and authorship information
- Ensuring batch production quality and traceability (currently relevant to managing the DHR)
Congratulations, your device is on the market! Now you need to keep records about the batches that you manufacture, including unique device identifiers that can be cross-referenced back to the source.
-
- Enable real-time updates: Record manufacturing and quality control activities as they occur, continuously, to ensure completeness.
- Prioritize traceability (again!): At this stage, traceability refers to materials, components and manufacturing processes used to manufacture each batch of your devices.
- Prompt correction: Any problems in manufacturing that result in quality issues or deviations from the correct specifications or procedures should be identified and corrected efficiently, with documentation to show how they were resolved.
How can QMSR, DHF, DMR, DHR software help?
Our team at Scilife can help you prepare for the new rules outlined in QMSR, and get your current DHFs, DMRs, DHRs, and MDFs in order. We also provide a DHF, DMR, DHR software (our document management system) for maintaining, updating, and synchronizing your complete documentation.
The FDA mandates manufacturers to keep the latest, approved version of all documents within the DHF and DMRs, along with a full version history. In order to meet this requirement, you need an organized, accessible, and secure place to house these documents.
Choosing the right digital DHF, DMR, DHR software is crucial for easy document and version control. Consider a fully customizable platform so that you can revise and synchronize it to meet your needs.
With the right QMS software, you can fully digitize the record-keeping of the design and production of your medical devices and keep your documents audit-ready, with little to no additional effort. This will not only save you money and time but also provide peace of mind while you focus on advancing your device throughout its lifecycle.
Consider these crucial features when choosing a document management system:
- Creating projects
- Creating document templates and getting approval for the templates
- Defining the contents of critical files at the beginning of each project
- Populating documents with approved content automatically
- Providing a version history for each document
- Having the latest approved files (DMFs, DMRs, and DHRs) collated and available to auditors
Conclusion
So, what is the best way to future-proof your medical device quality management documentation?
It starts with a robust (preferably digital) QMS. It continues with team awareness of what US regulations require and how they are changing in 2026 (moving from DHF, DMR, DHR to MDF), and it is backed up by rigorous, formal record-keeping practices that show how your medical device was designed, validated, and traceably produced to a consistent standard.
Discover how our medical device QMS can help keep your medical device documentation seamlessly connected and under control!