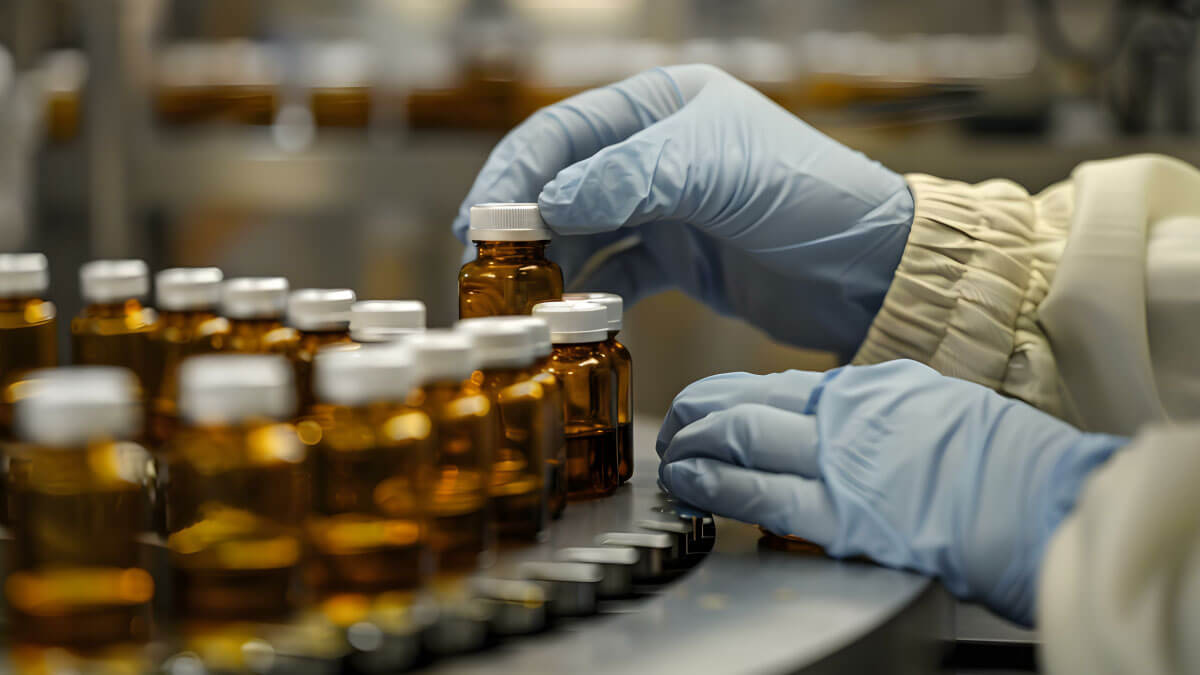
Good Manufacturing Practices (GMPs) have been the cornerstone of quality assurance in pharmaceuticals and medical devices for decades. These guidelines ensure that every product, from medicines to medical devices, is consistently produced and controlled to the highest quality and safety levels.
GMP standards cover all aspects of production, from starting materials, premises, quality assurance, testing, and equipment to staff training and personal hygiene. Specialists must ensure these guidelines are followed meticulously at each stage.
However, as technology evolves, so must current Good Manufacturing Practice (cGMP) standards.
This shift isn’t just for manufacturers. It is shaking up the entire pharmaceutical supply chain, from wholesalers to distributors. Whether you’re in quality assurance, regulatory affairs, or a leadership role, staying ahead of these trends is key to maintaining compliance and staying competitive.
Organizations must prepare for a landscape increasingly defined by automation, digital transformation, and stringent quality management systems. This blend will help companies not only meet regulatory demands but also stay ahead in terms of efficiency, compliance, and quality.
The incorporation of advanced technologies into GMP protocols presents both opportunities and challenges, demanding ongoing training and adaptation within the workforce.
In this post, we’ll explore how emerging technologies are shaping the future of GMP compliance, and we’ll share practical tips for professionals looking to prepare for this rapidly changing landscape.
How technology is shaping the future of compliance with GMP standards
The world of pharmaceutical manufacturing is undergoing a massive shift. The way we produce and monitor products is no longer confined to traditional methods. Technology is creating new possibilities for better compliance, faster production, and higher-quality products.
Using a simple analogy, consider yourself running a kitchen where you must bake the same cake over and over again while maintaining excellent quality.
In the beginning, you rely solely on your senses - taste, smell, and sight - to ensure that everything is right. What if you could use smart tools to monitor the temperature of the oven, monitor the moisture in the air, or even predict when ingredients are about to spoil?
That’s what technology is doing for pharmaceutical manufacturing—helping us automate, monitor, and optimize production so that nothing is left to chance.
Regarding compliance, the term current Good Manufacturing Practices (cGMP) emphasizes the importance of current standards, current processes, and current technologies in GMP regulations. This designation reflects the need for continuous updates to align with recent technological advancements and evolving safety standards.
The advent of smart manufacturing, a critical component of Industry 4.0, in 2011, as well as disruption technologies such as artificial intelligence, big data, deep learning, and the Internet of Things (IoT), has enabled organizations to automate processes, monitor operation real-time, and make better decisions.
This has resulted in increased efficiency and cost savings for the life sciences.
Key technologies driving the future of GMP
Now, let’s explore some of the key technologies that are transforming the way we meet GMP standards. These innovations aren’t just making compliance easier—they’re also opening the door to more efficient, reliable, and safer pharmaceutical manufacturing.
Digital transformation and AI
Think of Artificial Intelligence (AI) as the brain behind smart manufacturing. Just like how your phone can learn your habits and suggest things before you ask for them, AI in pharmaceutical manufacturing helps predict problems before they happen.
For instance, AI systems can analyze huge amounts of data from production lines and identify patterns—like detecting a slight vibration in a machine that could lead to future breakdowns. This predictive power allows manufacturers to fix issues before they affect product quality, saving time, money, and headaches.
Artificial intelligence has also revolutionized drug discovery by predicting the success rate of new compounds, which enables faster development of lifesaving medications. Despite not directly affecting manufacturing, this acceleration impacts production planning and scaling throughout the entire pharmaceutical lifecycle.
Recommended learning: Discover the countless applications of AI in the pharmaceutical industry and how you can leverage this technology.
Real-time monitoring and process optimization
Imagine having a personal assistant who can monitor every part of the production process in real time. This is exactly what IoT devices do in pharmaceutical manufacturing. They can measure everything from temperature and humidity to particle levels in the air. These devices ensure that the production environment is always optimal, reducing the risk of contamination and ensuring consistent product quality. It’s like having eyes and ears on every part of the operation, all day long.
Blockchain for transparency
Blockchain may sound complex, but at its core, it’s about building trust. This innovative technology creates an immutable, transparent, and secure digital ledger that enhances trust and traceability across the pharmaceutical industry.
But, how does blockchain work?
Once data is entered into the blockchain, it cannot be modified or deleted, safeguarding data integrity throughout the product life cycle. The decentralized network stores data across multiple nodes, making any unauthorized alterations immediately detectable. Each block is linked to the previous one via a cryptographic hash, creating a secure and transparent audit trail.
Think of it like a digital notepad where every action—whether it’s tracking raw materials or recording a step in the production process—is written down permanently. This “notepad” can’t be changed or erased, making it easy to track every step of manufacturing.
The benefits are substantial: blockchain enhances recall management, prevents counterfeiting, and boosts patient safety. By ensuring transparency and security, it helps pharmaceutical companies uphold GMP standards while fostering trust with regulators and consumers.
Robotics and automation
Robots are no longer just sci-fi material; they’re revolutionizing how pharmaceuticals are made. Picture a robot that can handle delicate tasks like packaging pills or inspecting vials with extreme precision. These machines don’t get tired, don’t make mistakes, and can operate all day long. For GMP, this means fewer human errors, better precision, and higher overall efficiency.
Another example is bots. They can automatically review batch records, ensuring all required documentation is included and data
from different systems is consistent and within operational parameters.
Robotics can also perform complex operations that require precision beyond human capability, reducing contamination risks and ensuring adherence to quality standards. For example, advanced robotic systems with camera and tactile sensor technology are used for precise handling of sensitive items like syringes and vials, reducing breakage risks and enhancing safety.
Another example is in packaging. Robots efficiently package pharmaceuticals into containers or blister packs and apply labels with high precision, reducing errors associated with manual processes.
There is no doubt that automation increases throughput, reduces operational costs, and ensures greater accuracy in data collection and reporting. This not only leads to higher-quality products but also accelerates time-to-market.
By leveraging robotics, companies can also reduce manual intervention, and maintain more efficient, reliable operations that meet regulatory requirements with ease.
Continuous manufacturing
Continuous manufacturing is a transformative approach to traditional manufacturing processes, that provides uninterrupted production flows that enhance operational efficiency and product quality.
As opposed to conventional batch manufacturing, which involves discrete production runs, continuous manufacturing allows for real-time monitoring and adjustments, ensuring that products meet strict quality specifications while minimizing waste.
However, the transition to continuous manufacturing does not come without its challenges: high initial investment costs, the need for advanced technological integration, and resistance to change.
The implications of continuous manufacturing on GMP will be profound, as it promotes sustainable practices, improves product quality, and ensures compliance with evolving regulations, making it a desirable approach for the future of manufacturing.
Advanced analytics
Advanced analytics refers to sophisticated techniques and tools used to extract insights, predict future trends, and provide actionable recommendations from data.
In the context of GMP manufacturing, advanced analytics encompasses several key components and applications, including machine learning, data mining, predictive analysis, and statistical analysis. All these applications play key roles in optimizing manufacturing processes, enhancing quality control, reducing downtime, and improving supply chain management.
For example, by analyzing historical data and using machine learning algorithms, manufacturers can anticipate equipment failures before they occur. This proactive approach can reduce machine downtime by 30 to 50% and extend machine life by 20 to 40%.
Another practical example is process optimization. By assessing historical data and recognizing relationships among process steps, operations managers can fine-tune variables that impact production yield.
Virtual and Augmented Reality
Virtual reality (VR) and augmented reality (AR) are immersive technologies that can bring training and maintenance to a whole new level.
VR simulates real-life scenarios by creating fully immersive digital environments, while AR overlays digital information onto the physical world, enhancing real-time decision-making and task performance.
Imagine wearing glasses that display real-time instructions while you perform a task, helping you avoid mistakes and ensuring that every step is followed perfectly.
Cloud computing
Manufacturing has traditionally depended on on-premises systems, which were often outdated and rigid, limiting flexibility and adaptability. However, with the rise of Industry 4.0 cloud computing has gained significant traction in the GMP sector.
Manufacturing historically relied heavily on on-premises systems that were often outdated and lacked flexibility.
Industry 4.0, which integrates IoT, artificial intelligence, and advanced data analytics, further accelerated cloud computing's adoption.
Cloud computing will redefine good manufacturing practices in the coming years. As industries evolve, leveraging real-time data and advanced analytics will become increasingly critical for maintaining a competitive edge.
For GMP, cloud computing offers substantial benefits. Its key strength lies in the ability to gather and integrate vast amounts of data from multiple sources. This real-time data integration enables manufacturers to gain actionable insights, allowing them to make informed decisions faster.
Cloud-based systems also support better data accessibility and collaboration, helping to streamline processes, enhance compliance, and improve overall operational efficiency.
Cloud solutions, such as electronic Quality Management Systems, are one example of how data and quality processes can be moved from standalone servers to the cloud. This shift allows for seamless integration of diverse systems, enabling better data sharing and collaboration across different sites.
By adopting cloud computing, pharmaceutical companies can stay agile, continuously monitor quality, and ensure they meet GMP requirements while responding more effectively to regulatory changes.
Scilife tips
As pharmaceutical manufacturing rapidly evolves, staying ahead of the curve is essential for quality professionals who are tasked with maintaining high standards while adapting to new technologies.
Here are some practical tips to help you stay ahead and ensure continued compliance with GMP standards:
Embrace digital transformation
Don’t shy away from new technology. Tools like AI and real-time monitoring systems are becoming essential for maintaining high-quality standards. They can help you spot issues early and make data-driven decisions that improve compliance and efficiency.
Invest in continuous training
As new tools and systems come into play, your team needs to keep up. Continuous learning should be a priority to ensure that everyone can effectively use new technologies while adhering to GMP standards.
The goal is to cultivate a culture of quality through regular education and training, audits, and assessments in order to address potential risks in a proactive manner. Ensure your staff stays updated on new systems, tools, and regulatory changes. This not only helps them adapt to advancements like automation and robotics but also ensures they can implement these tools while maintaining strict adherence to GMP standards.
Additionally, as sustainability concerns rise, aligning GMP practices with environmental responsibilities has emerged as a critical component of modern manufacturing strategies.
Adopt automation and robotics
Automation can take over repetitive tasks, reducing human error and increasing productivity. It can also free up your team to focus on more critical activities like quality oversight.
Leverage real-time data analytics
Cloud-based platforms, such as Scilife’s eQMS, allow you to monitor your quality processes in real-time, making it easier to address potential risks before they escalate into bigger issues.
Stay updated with regulatory changes
Regulatory bodies are continuously evolving to accommodate these new technologies. Make sure your team is always in the loop with the latest GMP guidelines and trends to avoid falling behind. Maintaining open communication with regulatory bodies ensures smoother audits and inspections.
Conclusion
The future of pharmaceutical manufacturing is here, and technology is at its core. By embracing digital transformation, automation, and real-time analytics, companies can not only improve compliance but also enhance operational efficiency.
The core message is clear: adaptation is vital.
To succeed in this evolving landscape, continuous learning and a proactive approach to adopting new tools will be critical. The companies that stay ahead will be those that don’t just see GMP as a requirement but as an opportunity to innovate and improve every aspect of their operations.
In this fast-paced industry, adaptation is not just necessary—it’s the key to thriving.
Key Takeaways:
- Continuous training must be a top priority. As technology rapidly evolves, so should your team’s skills. Investing in ongoing education ensures your workforce stays sharp, adapts to new tools, and keeps pace with regulatory changes.
- Automation and robotics aren’t just about speeding things up—they're game changers in reducing human error, boosting operational efficiency, and ensuring consistency across every production line.
- Real-time insights are like having a constant pulse on your operations. Cloud-based platforms help you make smarter, faster decisions by seamlessly integrating vast amounts of data, right when you need it.
- The regulatory landscape is evolving, and staying ahead means more than just compliance—it’s about being proactive. Regularly review updates to GMP standards to ensure you're always in alignment with the latest standards.
- The future belongs to companies that don’t just adopt new technologies but build a culture of innovation and continuous learning. Those who adapt, innovate, and remain compliant will thrive in the rapidly evolving world of pharmaceutical manufacturing.