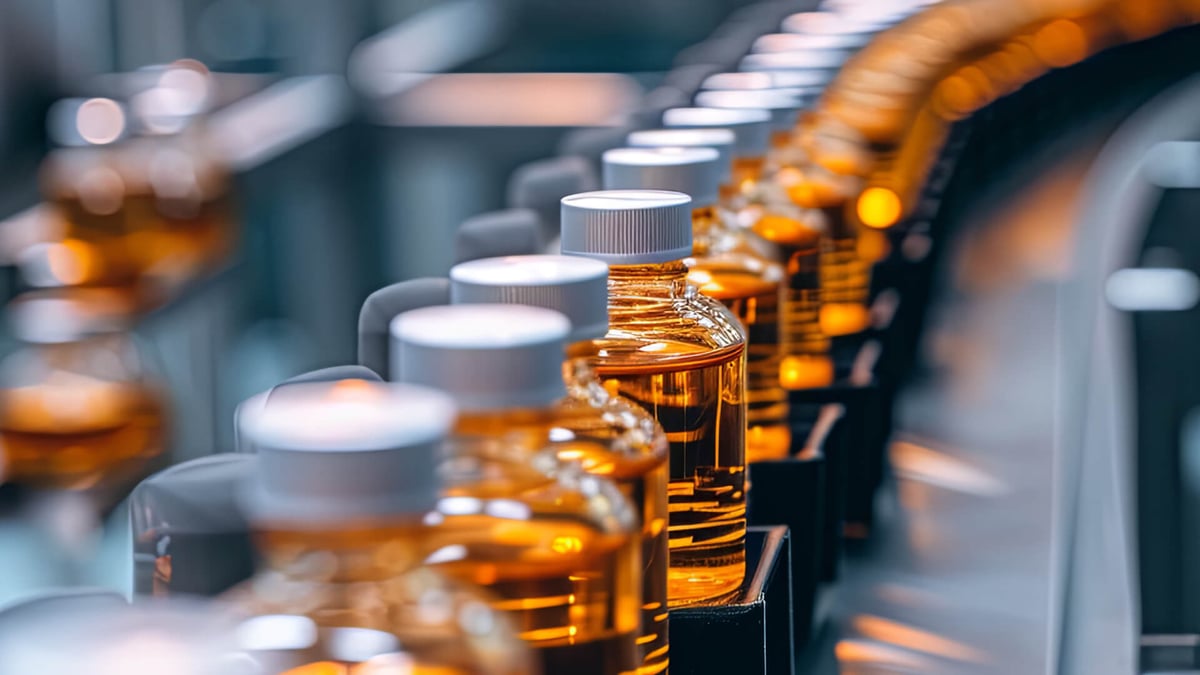
GMP stands for “Good Manufacturing Practices.”
In life sciences manufacturing, a buzzword you'll often hear is "Good Manufacturing Practices," commonly known as GMP.
But what exactly does it entail? This piece will outline the five main components of GMP and explore how they ensure the quality and safety of your products, from medical devices to pharmaceuticals. If you'd like to learn how GMP links to other key pharmaceutical regulations, go to our comprehensive QMS in pharma guide.
What Is GMP?
The complexity of GMP: More than meets the eye
At its core, GMP is a comprehensive manufacturing system designed to ensure product consistency and quality. It encompasses a multitude of facets, from hygiene and sanitation to quality management, all with the goal of mitigating and ideally eliminating significant risks such as cross-contamination, mislabeling, and process failures. Areas that play an active role in the GMP guideline include:
- Sanitation and hygiene
- Building, facilities, and equipment
- Raw materials
- Quality management
- Personnel
- Complaints
- Documentation and recordkeeping
- Validation and qualification
-
Inspections and GMP audits
By focusing on the above areas, achieving GMP compliance translates into products that are:
- Of consistent, high-quality
- Designed for their intended use
- Able to meet the marketing authorization or clinical trial authorization
Implementing Good Manufacturing Practices (GMP) has numerous advantages. By minimizing waste, it enhances productivity and profitability while mitigating risks associated with recalls, compliance issues, and other problems. As a result, GMP acts as a protective shield, safeguarding both life sciences companies and customers throughout the entire manufacturing process, ensuring top-notch product quality from start to finish.
Watch this video course for an easy-to-follow introduction to GMP! In Part 1, we’ll guide you through the 9 sections of the GMP guidelines for medicinal products."
GMP vs. cGMP: Splitting hairs?
You might be familiar with both GMP (Good Manufacturing Practices) and cGMP (current Good Manufacturing Practices). While GMP and cGMP (current Good Manufacturing Practices) are often used interchangeably, there's a subtle difference. GMP is the basic FDA regulation set forth to make sure manufacturers are being proactive in developing safe and effective products.
In contrast, cGMP advocates for continual improvement, prompting manufacturers to keep their systems and technologies current, thereby upholding the highest quality standards.
It’s important to note that while cGMP regulations feature a number of practices focusing on multiple manufacturing phases (and on several aspects of quality), these are just the minimum requirements organizations have already implemented in their quality assurance and risk management processes.
Recommended learning: Curious to learn more about the differences between GMP vs cGMP? This blog will explain everything!
So what, exactly, does compliance entail? Which regulatory bodies oversee these standards? The next section will provide an overview of the specifics surrounding GMP compliance.
Regulations ensuring Good Manufacturing Practices
The cGMP regulations, in accordance with FDA guidelines, are designed to certify the strength, quality, and purity of life sciences companies’ products. Manufacturers are expected to conduct regular inspections of their processes, implement consistent quality management systems, source the highest quality raw materials, and detect and investigate any product deviations. They must also maintain reliable equipment and facilities while strictly adhering to well-documented management and manufacturing procedures.
While the FDA oversees cGMP regulations in the U.S., the European Medicines Agency (EMA), conducts GMP inspections in Europe, ensuring the harmonized interpretation of GMP requirements across member states.
These requirements encompass the essential task of prioritizing and harmonizing the five key components of GMP.
The 'Five Ps': An overview of GMP's main components
GMP revolves around five core components or the "Five Ps":
Products
GMP underscores the quality of raw materials used in manufacturing. All products must comply with a specific master formula free from deviations throughout the manufacturing process, supported by a robust quality assurance system featuring regular testing and constant comparisons is imperative - complete with clear specifications at every production phase.
People
The success of GMP lies in the hands of well-qualified, well-trained individuals. Emphasis is placed on regular training in sanitation, recordkeeping, labeling, and equipment handling. Though training is an investment, it can make all the difference from a quality assurance perspective. All team members must strictly follow manufacturing regulations, with each individual fulfilling a specific role. Regular performance assessments and frequent evaluations will elevate competency.
Processes
It's crucial for manufacturers to strictly adhere to, and document, all manufacturing processes. As auditors regularly inspect laboratories and other facilities for consistency and quality, documentation is a key compliance factor. Manufacturers can take this a step further by keeping a written framework of the entire manufacturing process and distributing these materials to all team members. Here too, frequent evaluations are key from a compliance standpoint.
Procedures
Essentially the guidelines for executing processes, procedures need to be up-to-date, and employees need to be well-versed in them. A procedure is a series of guidelines needed to perform a process (with the goal of generating a specific result). During audits, manufacturing procedures are highly scrutinized. Utilizing outdated technology could jeopardize compliance. Procedural consistency can help mitigate this. Employees should fully understand the procedures they must follow.
Premises
The conditions of facilities, laboratories, and equipment are crucial for ensuring safe and effective manufacturing. Adequate maintenance, cleanliness, and a system for timely repairs all contribute to consistent results, lower the risk of equipment failure, and ensure timely repairs. Reducing product variations is the end goal here, as is protecting patients, customers, and team members from operational issues onsite.
How quality management software can help you with the 5 Ps of GMP
Adhering to the five main components of Good Manufacturing Practice can help you improve operations by reducing waste and preventing mistakes that can lead to recalls and other quality issues.
However, achieving true excellence requires more than just compliance. A sophisticated QMS software solution takes your GMP efforts to the next level by building a strong foundation for robust quality management. It streamlines processes, ensures consistent compliance, and transforms quality management into a competitive advantage—making it an indispensable tool in your journey toward GMP compliance.
Ultimately, an eQMS is the best tool to define and control every aspect of the 5 Ps across your organization and workforce. Here's a quick overview of some of the ways quality management software makes this possible:
How an eQMS helps products
- Integrates supplier evaluation and performance tracking tools to assess and manage the quality of raw materials and parts, ensuring they meet required standards.
- Centralized tools track and resolve customer feedback related to product quality.
- Features like calibration and maintenance tracking ensure equipment is properly maintained to support consistent product quality.
- Compliance tools help ensure adherence to industry regulations such as FDA 21 CFR Part 820, CFR Part 210, 21 CFR 211, EU GMPs, and ISO 9001.
How an eQMS helps people
- Centralized training data ensures that all personnel are up-to-date on the latest procedures and regulations.
- Tools within the eQMS provide role-based access and responsibility assignment, ensuring individuals are accountable for maintaining quality standards.
- Includes automated reminders for ongoing training and certification renewals, supporting compliance continuity.
How an eQMS helps processes
- Process mapping tools and workflow automation define, monitor, and ensure compliance with industry standards across all manufacturing processes.
- Includes tools for investigating quality defects and tracking corrective and preventive actions to prevent recurrence.
- Integrated risk management modules assess and mitigate risks across the manufacturing processes
How an eQMS helps procedures
- Centralized document management systems in the eQMS help define and document Standard Operating Procedures (SOPs), ensuring version control and preventing the use of outdated procedures.
- Seamless change management ensures that updates to procedures are evaluated and validated before implementation.
- Features like automated approval workflows and digital signatures streamline the review and approval process, ensuring proper compliance.
- Document control ensures documents are consistently updated, maintaining compliance and accuracy across all procedures.
How an eQMS helps premises
- Automated scheduling, planning, execution, and follow-up of internal and external audits ensure nothing is missed.
- Data analytics and reporting capabilities offer insights into process performance and compliance.
- Corrective actions are monitored over time, ensuring ongoing compliance and continuous performance improvement.
- Maintenance and calibration schedules for equipment and facilities are managed to contribute to a well-maintained and compliant manufacturing environment.
Take a look at the infographic below for a quick overview of how quality management software can help you with the 5 Ps:
Achieving GMP compliance: The road ahead
Achieving GMP compliance involves a commitment to the Five P's and a dedication to the following practices:
- Drafting clear, specific procedures.
- Ensuring the cleanliness and maintenance of all equipment.
- Performing regular compliance audits.
- Conducting thorough competence analysis before hiring.
Key principles of GMP
To summarize our discussion, here is a concise overview of the fundamental principles that underpin GMP:
-
- Creation and enforcement of Standard Operating Procedures (SOPs).
- Comprehensive documentation of all procedures and processes.
- Validation of SOP effectiveness.
- Development and implementation of efficient working systems.
- Development of employee competencies.
- Regular maintenance of systems, equipment, and facilities.
- Prioritizing cleanliness to prevent contamination.
- Ensuring quality is central to the design, development, and manufacturing workflow.
- Creation and enforcement of Standard Operating Procedures (SOPs).
GMP compliance is a continuous journey, not a destination. Regular audits, swift identification of potential deviations, and corrective actions are all part of this process. Embracing a culture of ongoing improvement and having a team that understands and implements the principles and components of GMP are the first steps towards ensuring 'Good' isn't just a target in manufacturing - it's a standard.
One step forward: Leveraging QMS software for GMP audits and inspections
Audits and inspections are a crucial part of the GMP landscape. They provide a systematic and independent examination of a company's quality system to ensure adherence to the set guidelines and regulations. Scilife's Smart QMS software plays a pivotal role in making these audits and inspections not only manageable but efficient.
One significant aspect of this is the QMS software's capability to maintain comprehensive and accessible records. Documentation is a cornerstone of GMP, and during audits and inspections, easily retrievable records are essential. Our software ensures complete traceability, helping your company withstand the scrutiny of any audit or inspection with ease.
Moreover, the ability to manage deviations, CAPAs, and change controls within the QMS software enables businesses to demonstrate their commitment to continual improvement - a principle at the heart of cGMP. With real-time data, automatic alerts, and detailed audit trails, our QMS software ensures that your company is always ready for an audit, minimizing non-compliance risks and fostering a culture of quality.
Overcoming GMP challenges in pharma and medical device industries with QMS software
GMP compliance comes with its share of challenges for the pharma and medical device industries. From stringent documentation requirements to managing personnel training and ensuring product consistency, there is an array of complex issues to navigate. Our QMS software is a game-changer in overcoming these challenges.
The first hurdle is often documentation. Our QMS software offers streamlined, centralized documentation management to ensure every process, procedure, and product detail is meticulously recorded and easily retrievable. This not only simplifies audits but reduces the risk of non-compliance due to lost or inaccessible records.
Training personnel and ensuring they remain updated on the latest regulations and procedures is another major challenge. Our QMS software aids in the scheduling, tracking, and documenting of training sessions, maintaining a competent workforce that's up-to-speed with the latest in GMP.
Ensuring consistent product quality across different batches, sites, or even countries can be tricky. With its robust tools for managing product specifications, supplier quality, and process changes, our QMS software aids in maintaining the consistency necessary for GMP.
Overall, the right QMS software can turn challenges into opportunities, helping pharma and medical device companies navigate the complexities of GMP compliance and ensuring the highest standards of quality.
The role of QMS software in ensuring GMP compliance
In the complex landscape of Good Manufacturing Practices (GMP), companies are continually seeking strategies to streamline their processes and bolster compliance. Quality Management System (QMS) software emerges as a powerful tool in this quest, providing a robust and efficient solution to manage the complex nuances of GMP compliance.
Our QMS software is designed to act as a central hub for all quality-related activities, encapsulating every facet of the GMP structure. It integrates seamlessly with the operations of pharma and medical device companies, allowing for real-time tracking and management of quality data across multiple departments and facilities. A QMS aids in the unification of quality management processes, from complaint handling and non-conformance tracking to document control and employee training. With built-in tools for risk assessment, our QMS software provides a proactive approach toward potential quality issues, allowing businesses to maintain a robust state of control, a critical aspect of GMP compliance.
Moreover, the software aids in maintaining comprehensive documentation and recordkeeping, key tenets of GMP, enabling effortless traceability that eases audit preparedness and ensures regulatory readiness. The automation capabilities of our QMS software minimize manual errors, ensuring a higher level of data integrity and adherence to the stringent requirements of the FDA and EMA.
Conclusion
Good Manufacturing Practices (GMP) is a comprehensive manufacturing system that ensures product consistency and quality by addressing 5 key components: products, people, processes, procedures, and premises. GMP compliance offers numerous advantages, including enhanced productivity, profitability, and risk mitigation.
Quality Management System (QMS) software plays a vital role in enhancing GMP compliance by managing documentation, training, processes, procedures, and premises. It helps overcome challenges in the pharma and medical device industries and ensures the highest standards of quality. Implementing GMP and leveraging QMS software contributes to a culture of ongoing improvement and the attainment of top-notch manufacturing standards. So, if you’re looking for a QMS to enhance GMP compliance, feel free to reach out to us at Scilife.