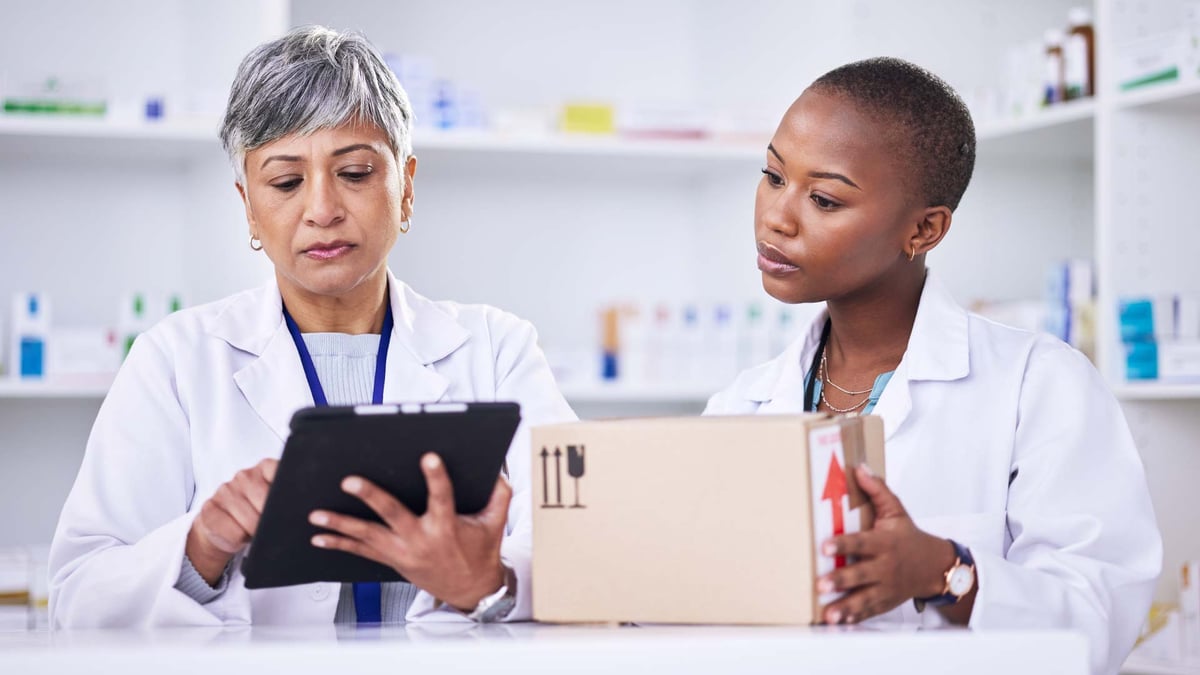
In the history of civilization and economic development, several industrial revolutions have brought about profound paradigm changes in society, economics, and culture, reshaping industries, creating new opportunities, and raising living standards for millions of people worldwide.
The First Industrial Revolution, which took place in the 18th and 19th centuries, was characterized by the mechanization of production through the use of water and steam power.
The Second Industrial Revolution, occurring in the late 19th and early 20th centuries, saw the emergence of electricity, mass production, and the rise of the assembly line.
The Third Industrial Revolution, also known as the Digital Revolution, began in the late 20th century with the advent of computers and the internet, leading to the automation of many industries.
Finally, the Fourth Industrial Revolution, which we are currently experiencing, is characterized by the fusion of technologies, such as artificial intelligence, robotics, advanced digital solutions, and the Internet of Things, blurring the lines between the physical, digital, and biological worlds. This revolution is creating smart factories and driving efficiency, productivity, and agility in operations.
The purpose of this article is to explain how smart manufacturing ensures pharmaceutical product quality and consistency by detecting discrepancies or anomalies in real time.
In addition to addressing supply chain complexities related to raw material quality and inventory management, real-time oversight of production processes helps maintain high-quality standards across all batches and production lines.
What is Smart Manufacturing?
Smart manufacturing is a critical component of Industry 4.0. Unlike traditional manufacturing approaches, smart manufacturing goes beyond simple automation to enable autonomous and self-optimizing production processes. It is a modern approach to manufacturing that leverages advanced technologies and data analytics, enabling real-time monitoring, analysis, and decision-making, leading to efficiency, and achieving higher levels of operational excellence.
What is a Smart Factory?
Another key concept within Smart Manufacturing is the idea of a smart factory. A smart factory is a cutting-edge manufacturing facility characterized by its high degree of digitization and connectivity. It seamlessly integrates advanced technologies like sensors, robotics, and artificial intelligence (AI) to enable real-time monitoring, analysis, and optimization of production processes. This integration fosters an environment where operations can autonomously adapt and optimize, ensuring peak efficiency and quality in manufacturing operations.
Current challenges and solutions in the pharma supply chain
The pharmaceutical industry faces several challenges in its supply chain:
Real-time visibility and tracking: Manufacturers and distributors need immediate access to information about product stock levels, conditions, and transit status to be more agile. It is not just about knowing where the shipments are, but also about requiring real-time data on demand trends, customer preferences, and market conditions. This information allows them to make informed decisions regarding inventory management, production planning, and supply chain optimization, ultimately improving their overall operational efficiency.
A good example is the integration of the Internet of Things (IoT) into inventory management. A real-time inventory tracking system ensures optimal stock management, reduces waste, and ensures availability. IoT can anticipate potential disruptions, ensuring smooth operations.
Overstocking and understocking: Maintaining appropriate stock levels is vital for prompt delivery, but excessive stock can lead to increased costs, product spoilage, and inefficiencies. There is also the bullwhip effect, which exacerbates this issue, causing mismatches between orders and demand.
Therefore, striking a balance in stock levels, particularly during emergencies, is critical to avoid increased costs, storage issues, product wastage, and supply shortages. A good example is advanced inventory systems with real-time visibility solutions that provide crucial data on inventory levels. This optimization reduces waste, and anticipates potential disruptions in the supply chain.,
Cold chain losses: Cold chain failures can have detrimental effects on product quality, efficacy, and patient safety. Maintaining specific temperature conditions throughout the supply chain is imperative to prevent damaged products and substantial financial losses.
Historically, the big challenge is maintaining temperature during the distribution of products requiring refrigerated conditions of 2-8 ºCelsius. In recent years, there has been an increase in products requiring controlled room temperature conditions and frozen conditions.
Several solutions are available. One solution is the use of active thermal systems, which use mechanical or electrical systems powered by an energy source, combined with thermostatic control of temperature. Another solution is the use of cost-effective passive thermal systems that use water/ice or dry ice to temper the product. However, neither of these solutions is perfect and each has its advantages and disadvantages. Active systems can be expensive to install and maintain, while passive systems can be difficult to standardize. Ultimately, the best solution depends on the specific product and its requirements.
In any case, temperature monitors, whether digital, chemical, or mechanical, provide monitoring of shipments while in transit. By equipping shipments with IoT sensors, manufacturers and distributors can gather real-time data on temperature, humidity, and location, ensuring that products are stored and transported under optimal conditions. This data can then be accessed remotely, providing the necessary information for agile decision-making and proactive response to any potential issues.
Counterfeit Medicines: Combating counterfeit medicines, particularly in developing countries, requires robust track-and-trace technologies and stringent regulatory measures to uphold product quality and patient safety.
Using 2D codes for serialization increases pharma supply chain security. This way, individual medicine packets can be identified clearly and tracked and traced more easily.
By staying informed when shipments deviate from their route or enter high-risk zones, real-time security alerts can also protect shipments against theft.
There is also blockchain technology, a distributed ledger structure that prevents counterfeit medicines, enhancing security, transparency, and traceability in the pharma supply chain. Using blockchain technology, data is stored securely and transparently on a decentralized network of nodes. This ensures that data cannot be manipulated after entry, making it extremely difficult for counterfeiters to tamper with information related to pharma products. The transparency provided by blockchain allows for full visibility into the movement of medicines, making it easier to detect fraud and identify weak links in the supply chain.
Over-reliance on a single region: Diversifying sourcing strategies and mitigating risks associated with over-reliance on a single region for drug components is vital to prevent supply chain disruptions stemming from conflicts, natural disasters, or trade disputes, thereby safeguarding customer satisfaction and product availability.
Smart manufacturing approach in pharma supply chain resilience
Using smart manufacturing in the pharma supply chain and product lifecycle, pharmaceutical organizations can achieve greater efficiency, quality, and agility.
In order to implement smart manufacturing principles within a factory, all plant components must continuously provide authentic data. With this data, plant conditions can be monitored securely, enabling early detection of anomalies well in advance of potential problems. Consequently, proactive countermeasures can be implemented to avoid costly plant downtime.
The challenge is usually ensuring that all of the critical factors of a process plant are captured. Here is where connectivity unleashes its full potential.
As an example, you may be able to access existing data sources from field devices from the control system. Components like temperature probes, pumps, compressors, and gears transmit valuable data via IoT sensors that allow you to conclude their operating condition. This data can then be used to optimize operations, improve predictive maintenance, and detect any potential problems before they become serious. Furthermore, connectivity can also provide valuable insights, enabling businesses to make better-informed decisions.
Smart manufacturing can also be applied to continuous manufacturing.
Pharmaceutical continuous manufacturing refers to the process by which raw materials are continuously fed into the manufacturing process, and the final product is continuously harvested, rather than being produced in batches. There are several advantages to this approach, including improved efficiency, reduced waste, and enhanced flexibility.
Continuous manufacturing reduces downtime between batches and eliminates batch processing which results in more streamlined operations, increased productivity, and reduced costs. Additionally, continuous manufacturing allows for real-time monitoring and control of the production process, so that product quality and consistency can be ensured. This represents a major opportunity for the pharmaceutical supply chain to modernize its operations and meet the challenges of today's evolving environment.
Conclusion
Smart manufacturing offers a transformative solution to the complex challenges faced by the pharmaceutical industry in its supply chain management. By leveraging advanced technologies such as IoT, real-time monitoring, and data analytics, pharmaceutical organizations can enhance efficiency, ensure product quality, and respond proactively to potential disruptions.
The key takeaways are:
- Real-time monitoring and data analytics enable early anomaly detection, allowing for proactive measures to prevent costly plant downtime.
- Connectivity through IoT sensors provides valuable insights into plant conditions, facilitating optimization of operations and predictive maintenance.
- Smart manufacturing enhances pharma supply chain resilience by enabling agile decision-making and proactive response to supply chain disruptions, ensuring product availability and customer satisfaction.
Discover how a smart QMS can help you navigate the current challenges of the pharma supply chain!