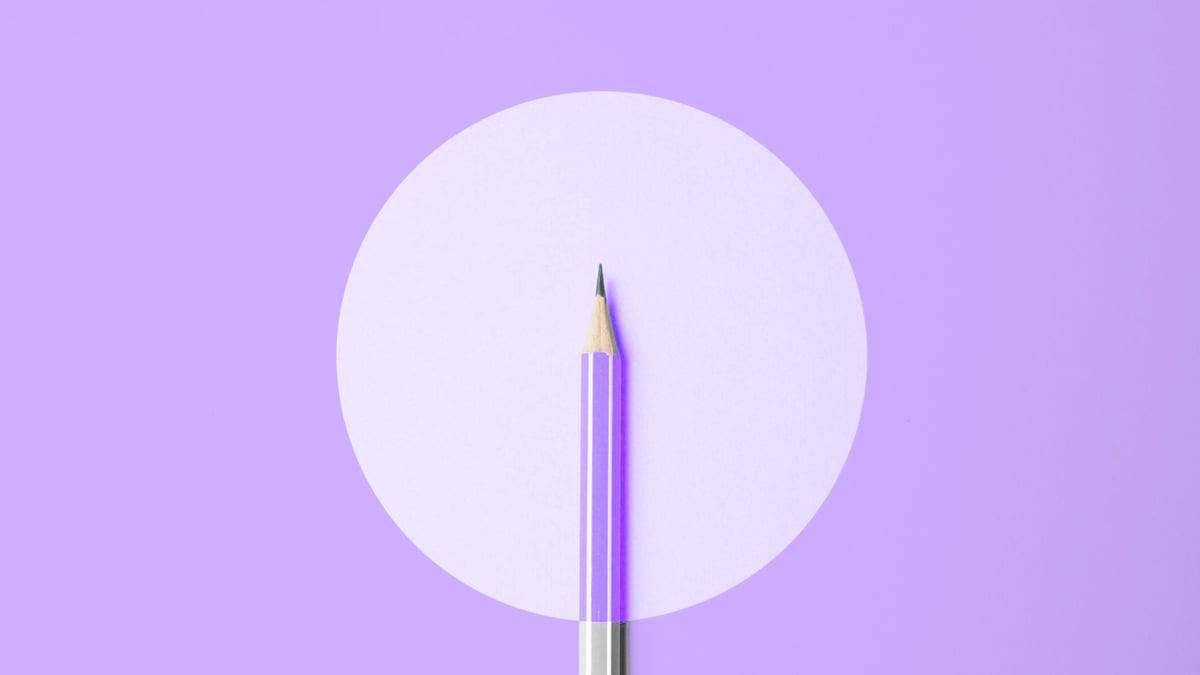
Standard operating procedures (SOPs) describe, well, the standard operating procedures of a company. They provide step-by-step instructions on how to perform the most common tasks at a company. When SOPs are efficient, they decrease miscommunication and compliance failures while increasing your tasks' efficiency, performance, and quality.
For medical device manufacturers, standard operating procedures that can prevent issues during conformity assessments, audits, or patient safety issues is paramount. Quality management regulations for medical devices, such as ISO 13485 Quality Management Systems for Medical Devices and 21 CFR 803, provide specific lists of SOPs that medical device manufacturers must establish. For example, ISO 13486:2016 requires SOPs for document control, record control, management review, design and development, sterilization validations, traceability, complaint handling, and reporting to regulatory authorities, to name but a few. ISO 13485 furthermore requires manufacturers to define, document, implement, provide training on, and maintain all the SOPs included in the quality management system.
Terms and Definitions
Standard Operating Procedure (SOP)
Practical-oriented instructions that provide broad and general guidelines for complex processes.
Work Instruction
Detailed step-by-step instructions for individual jobs and tasks within the overall process.
Policy
Overall framework and guidelines for behavior and decision-making
What should an SOP contain?
An SOP should describe and document how activities should be carried out to ensure consistency and efficiency and to support the highest possible consistent quality output. In essence, the SOP should describe what roles and actions are involved in the task, which methods should be used to perform the tasks, which tools and aids are involved in the task, the order with which to complete the task, and the input and output required for the task to be successful.
In contrast to work instructions, standard operating procedures describe tasks and sequences several people perform over time. The work instruction is an extension of the standard operating procedure, describing each job within the task in detail.
Standard Operating Procedure Template / Structure
SOPs can have any structure within the quality management system and current document control practices. Generally, you want to include the following sections:
- Formatting and provenance: all SOPs should be written and formatted similarly. Including the company logo, appropriate titles and document numbers, issue dates, review, and effective dates, and traceability helps ensure consistency and proper organization within the documents.
- Introduction: any SOP should include the purpose, objective, and scope of the SOP.
- Approvals: document owners should add their signatures and date of signing
- Table of contents
- Definitions and abbreviations: any acronym or abbreviation in the document should be defined to avoid ambiguity.
- Procedure: a description of the procedure and steps necessary to perform the task in question.
- Revision history: revision history is vital for traceability and ensuring the procedure you're reading is always up to date. There's nothing worse than learning a procedure only to find out it is not the current version.
- References and related documents
- Appendixes / attachments
How can I make my SOPs more effective?
An SOP should be clear, easily understood, and unambiguous. Vague expressions, science-speak, and making things more complicated than needed may lead to problems with performing the task as intended and larger issues, such as audit non-conformities, down the line.
Here are our best tips and tricks for making sure your SOP is as effective as possible:
Write your SOP for your end user
While the person writing the SOP might understand every step of the process and know the details of every product involved, the party performing the task may be a different person from a different department. When writing SOPs, it is important to be as objective as possible and see the steps from the outside. Consider how you would write the SOP if the person performing the task knows nothing about the product or process you're describing. Consider wording, expressions, which terms you use, and how precise you describe each step in the process. A good tip is to have someone completely unrelated, such as your partner or parents, read the procedure. You should be good to go if they understand most of it (they probably will need help understanding the technical bits).
Follow a clear structure in all your SOPs
Following the same format helps readers become familiar with the documents quicker and can help them interpret and follow the procedure consistently.
Avoid vague language and industry jargon as much as you can
Quoting regulations and guidelines word-for-word, using complicated or technical words when everyday words that can say the same thing exists, and using passive and boring language can confuse your reader and suck the motivation right out of them. Most regulations and guidelines are unclear or easily understood, so re-phrasing them in simpler language can help your reader know what they need to do. I once worked for a company with a complete quality management system – the problem was that the procedures were so convoluted that nobody understood what they were supposed to do. Making things simple and easily understood for your end-users will pay you back tenfold.
Keep careful track of document versions and revision history
Traceability is everything, especially during conformity assessments or audits. If the auditor can quickly understand which versions are used and which revisions have been made, you will automatically gain points with them without making much of an effort.
Use work instructions
When the standard operating procedure becomes too long and too detailed, use work instructions to provide detailed step-by-step instructions and annex them to the SOP. This is especially useful if your SOPs cover various languages or training levels – the SOP can act as a general document in the native language of the company while work instructions are translated and tailored to the population who will be using them. Always ensure the translation is accurate, traceable, and updated with the same frequency as the master (native) document.
Use visual aids
Flowcharts, diagrams, and images can help personnel understand a process in a way that pure writing cannot, especially in cases where the native language of the procedure is different than the local version. Diagrams and flowcharts can provide useful overviews and reference guides.
Conclusion
Adhering to SOPs is the best way to ensure consistency, efficiency, safety, and quality in your day-to-day organization operations. Efficient SOPs can also help mitigate risk and ensure regulatory compliance for all the departments involved. Especially for medical device companies who need to produce safe and efficient devices for their patients and users, SOPs are invaluable tools.
A correct use of SOPs is key to being fully compliant. Discover how Scilife Smart QMS can help you achieve it!