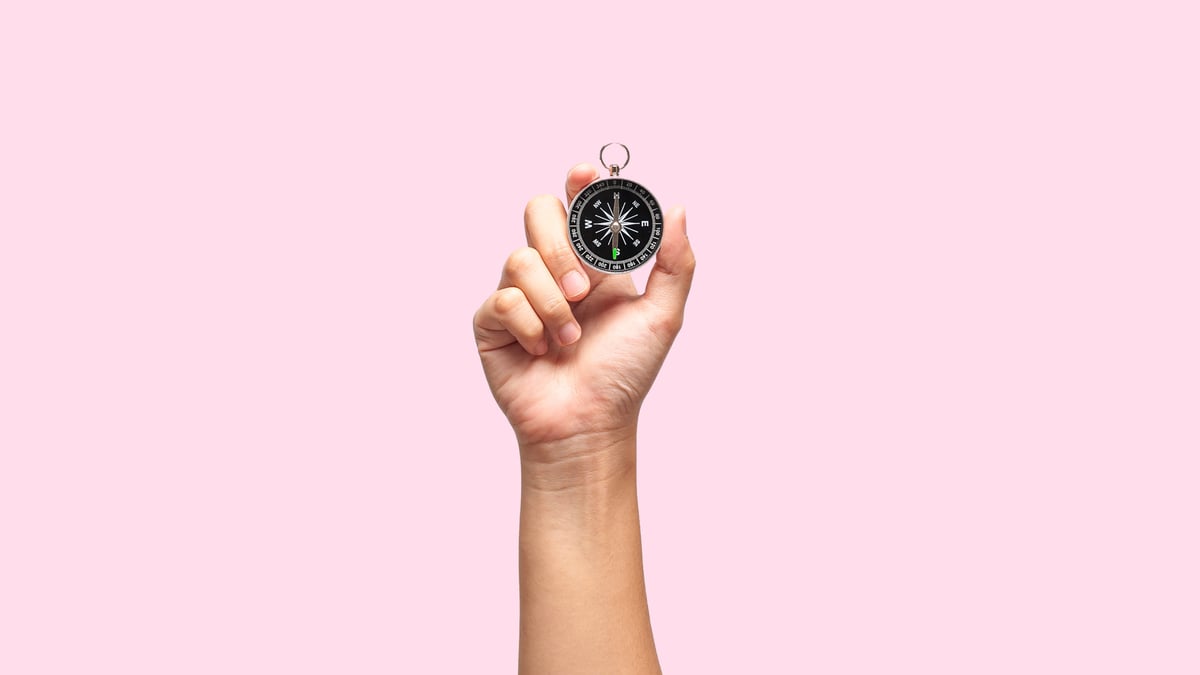
Are you worried about writing a change control document for organization-wide change? It’s normal that this can feel like a gut-wrenching process sometimes. After all, change management is no easy task! The bigger the organization, the more arduous the implementation process.
No matter how much we dread change, it is an inevitable part of our life. Older, redundant, and inefficient processes must be replaced with newer, specific, and efficient processes in every organization. That also makes it crucial to document any changes while answering the important questions: Why is it being changed, and how will it be changed? A document that contains all this information is called a change control document.
Such a document is even more crucial in the life sciences industry because of the strict scrutiny by regulatory agencies. A lousy change control document may lead to uncertain processes and lengthy discussions during regulatory audits. The following top five pointers are there to help you write a better change control document.
1. Poor Articulation
The number one challenge is to write as succinctly of a document as you can. The change control document should be self-explanatory and include all the necessary details:
What?
-
- Be specific about what is being changed!
- Are you changing the whole process or just a part of a process?
Why?
-
- Give the reason for change:
- Saving costs?
- Meeting organizational goals?
- Enabling faster decision making?
- Ensuring faster processing?
Advantages
-
- Remember the famous quote by James Belasco and Ralph Stayer: “Change is hard because people overestimate the value of what they have and underestimate the value of what they may gain by giving that up.”
- Tell your employees why they should not overestimate the advantages of the current process.
Risks
Objectively assess the adverse outcome associated with this change:
-
- What are the potential risks associated with the change?
- How will you measure the probability of possible risk factors?
- What is the estimated severity of the consequences?
- If the adverse outcome were to occur, what will your mitigation strategy be?
- Having a Failure Mode Effect Analysis template can help you be more precise in risk assessment and mitigation.
-
How?
- Are you going to implement the change in sequential stages or in one step?
- What resources will you need?
- What is the timeline for this?
- Who will be primarily responsible for implementing the change in each stage?
- What is the implementation deadline for each stage?
- Who will be responsible for individual tasks associated with the change?
- Who has the overall responsibility of making the change happen as a whole?
- Who will review, approve, and authorize the change control process?
2. Linking (and Finding) Documents
Many times, you may have multiple documents and processes that must be linked to the change control document. The change control document reader may not have access to them. Therefore, the reader may have to do the menial task of finding the linked documents and processes to make sense of the change control document.
For example, let’s say your company had a market complaint about the discoloration of tablets. Based on the market complaint, your internal team did a root cause analysis and discovered that the discoloration was due to improper packaging material. Therefore, as a corrective and preventive action, your team decided to change the packaging material of the tablets. Now, implementing this change in the packaging material of the tablet will require you to reflect the same in the standard operating procedures and the manufacturing processes linked to that specific product. Hence, you will need to connect the incident/deviation of the market complaint, corrective and preventive action document (CAPA), standard operating procedures in the document control software, and associated manufacturing processes with the change control document you will write.
Missing out on any linked document may leave your employees perplexed about what to do next. Not an easy task, right? Especially if you have a traditional paper-based Quality Management System! With Scilife’s eQMS, this process would be a breeze.
3. Who will bell the cat?
How will you know who is responsible for which task? And most importantly, who will keep them reminded about doing the tasks?
A clear responsibility assignment is vital to moving any change forward. In the absence of responsibility assignments, team members will keep gazing at each other to take the initiative.
In most situations, every change is associated with multiple small tasks dependent on different stakeholders. Therefore, every task associated with the one big change should be assigned to individual team members.
In a paper-based QMS, you can assign task responsibility to the team members, but you have no automated way to remind them of their tasks, unlike in the eQMS.
4. Remember the Important Dates
Every big change is implemented with a series of small changes. Depending on their interdependence, you can schedule these small changes on the same or on different dates. Therefore, defining a timeline for change implementation is essential to managing the transition.
However, remembering all important dates is almost impossible. If you are using an eQMS, you may find some relief in easily monitoring the dates on which the changes will take place.
At the same time, making changes in the original timeline due to unforeseen reasons is also very handy in an eQMS – unlike in a paper-based system where the handwritten document will become chaotic because of manual corrections in the timeline.
5. Managing Differences in Opinion
When working in big teams, a difference of opinion is quite likely. For example, if the authorizer for the change control document has a different view, then the authorizer may reject the change. The authorizer may ask you to articulate the change control document differently with some feedback in the form of comments.
Keeping track of all these conversations, which were deciding factors for the final form of the change control document, is another herculean task. However, if you are using a 21 CFR Part 11 compliant eQMS solution, you may have access to the audit trail of document changes along with the comments.
An audit trail consists of the date and time stamp along with the user details of the person who made changes in the document. This makes the process transparent for regulatory authorities and helps you avoid dependence on memory to answer such questions.
Additionally, an eQMS system can help you get rapid approvals as the document does not need to be physically transported for evaluation by multiple stakeholders. Instead, all changes can be seen in real-time from users across different locations.
Conclusion
You can easily make your change control document more precise and concise by avoiding these top five issues. Highlighting clear reasoning, possible advantages, better-managed risks, and clarity of actions can be crucial to implementing a successful change control process.
Scilife’s eQMS solution will empower you to better manage your change control documents. You will be able to track the document changes in real time and link the change control document with other relevant documents effortlessly.
As a result of good change control document, employees in your organization will be more adaptive to the new changes. Employees will no longer dread spending time on change control documents. In fact, we see active participation from employees increase after a Scilife eQMS implementation. Employees themselves will make the change happen and stick longer!
Discover how to automate your change control processes with Scilife. You can also link it to Document Control and CAPAs solutions!