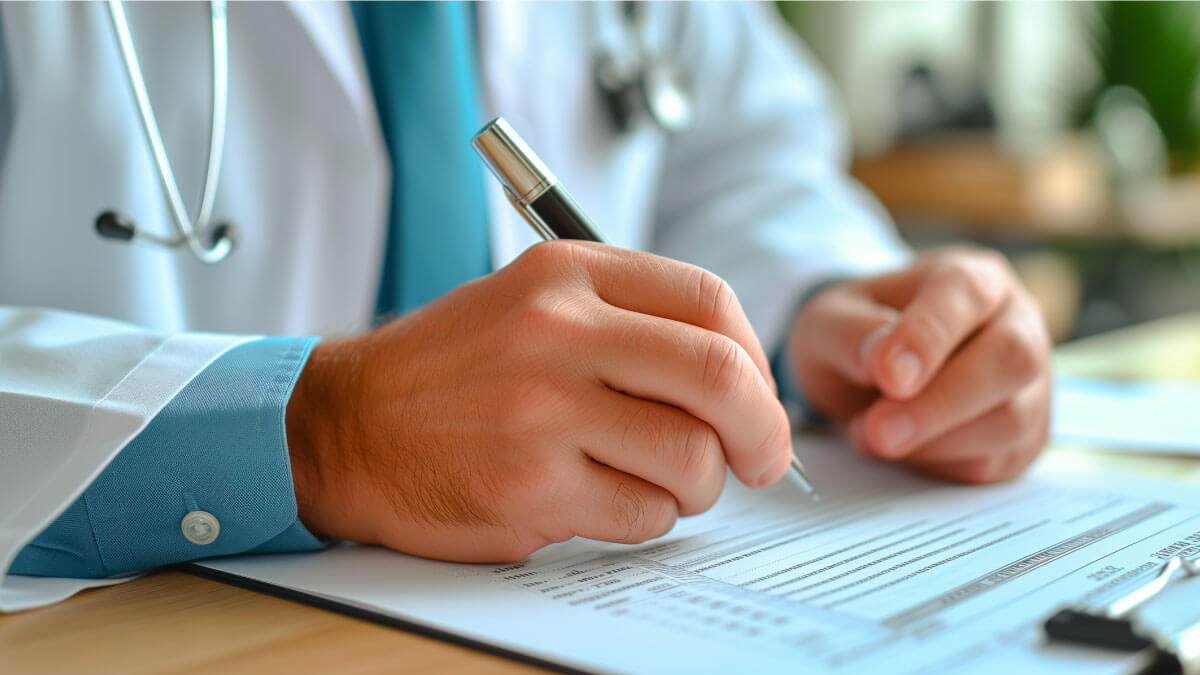
In life sciences, especially if you’re in the medical device industry it becomes harder to manage projects in accordance with your company’s quality management system. Companies design and/or develop products every day to improve their existing products and address their customer needs. As a medical device company, you should have a process for quality planning that defines the projects needed for quality throughout the product life cycle.
You should also be aware that it is required by the FDA and ISO 13485:2016. With a well-written quality plan in place, you'll enable your team with the quality management system framework to put high-quality medical devices to the market.
In this post, we’ll cover what a quality plan is, why it is important, and the steps to write a good quality plan for a medical device.
What is a quality plan?
A quality plan is a document, or several documents, that together outline quality policies, procedures, practices, guidelines, resources, and standards for processes, product(s), or organization, and provides details on how these quality standards will be achieved and controlled. The inputs, outputs, and deliverables differ widely depending on the industry, the size of the organization, the type of product, and other factors.
Joseph M. Juran defines three basic managerial processes required for quality. It’s called the Juran trilogy, the three processes are quality planning, quality control, and quality improvement. The initial activity is quality planning.
Juran’s quality planning consists of the following steps:
- Determine who the customers are and what their needs are.
- Translate those customer requirements into products with desired features
- Develop processes that enable them to produce the product with desired features
- Transfer the process, with appropriate controls, to operations.
Now let’s read how the FDA and ISO define quality planning;
FDA 21 CFR 820.20(d) - Subpart B—Quality System Requirements Management responsibility - (d) Quality Planning.
“Each manufacturer shall establish a quality plan that defines the quality practices, resources, and activities relevant to devices that are designed and manufactured. The manufacturer shall establish how the requirements for quality will be met.”
ISO 9000:2015 - Quality management systems - Fundamentals and vocabulary
Quality planning is part of quality management, focused on setting quality objectives and specifying necessary operational processes, and related resources to achieve the quality objectives. Additionally, establishing a quality plan can be part of quality planning.
ISO 10005:2018 - Quality management — Guidelines for quality plans
The specification of the actions, responsibilities, and associated resources to be applied to a specific object modified.
Recommended learning: Gain expert tips for writing flawless SOPs in our free guide!
How to write a quality plan
A well-written quality plan enables projects to run smoothly. But how? Now let’s learn how to create a good quality plan. There are specific steps to follow. Here you will find all the key elements of a strategic quality plan. You should start by determining the quality standards and what procedures you’ll use to check specifically for your medical device to meet the criteria.
A medical device strategic quality plan ties together your organization’s quality goals with activities. A quality plan can demonstrate your strategic quality goals into actions, and tie your expected outcomes to processes, procedures, and practices. In simple words, the quality plan shows what you plan to do, who will do it, and how it will be done. While creating this plan, there are no certain rules to follow, as it depends on the complexity of your scope and your product(s).
Typically, a quality plan includes the following detailed information:
- An overview or introduction of the project or process detailing the background, need, scope, activities, and important dates or deadlines
- Objectives to be achieved
- Process steps that define the operating practice or procedures
- The organizational structure or organizational chart that specifies required roles including externals
- Roles, responsibilities, and qualifications necessary to fulfill stated duties
- Allocation of responsibilities, authority, and resources during the different phases of the process or project
- Specific documented standards, practices, procedures, and instructions to be applied
- Supplier standards (e.g., specify the standards the prospective suppliers must meet before they can bid on a contract, such as ISO 9001:2015)
- A list of qualified suppliers
- Performance standards and how performance will be documented
- Acceptance criteria
- Deliverables
- A feedback mechanism for internal and/or external customer feedback
- Suitable quality control, testing, inspection, examination, and audit programs at appropriate stages
- A documented procedure for changes and modifications to a quality plan as a process is improved
- A method for measuring the achievement of the quality objectives
- Training requirements (e.g., overview, job-specific, or refresher training)
- Corrective action and preventive actions, including the person(s) responsible for CAPA
- Suggested corrective action
- Other actions necessary to meet the objectives
- Required notifications
- Any references or related materials, including performance ratings or performance reports
Step 1 - Determine the Scope
Determine the project title and draft a brief statement for the scope. The scope of your quality plan should be clearly defined by emphasizing project details including project overview, scope of services, and risks that are specific to the project per your organization’s mission and strategic direction.
Typically, the scoping phase shapes the overview of the quality plan. Additionally, if the quality plan is about a new device, it should refer to standard operating procedures, product-related policies, and processes.
Step 2 - Resources
Every quality plan should contain certain resources to execute the plan smoothly. Identify resources needed and specify the type and amount of resources including:
- People
- Materials, products, or services,
- Infrastructure and environment for the operation
- Equipment for the operation, measurement, and monitoring of processes.
Make sure you consider all aspects of your project and list and make them ready for use before starting to implement your project. Having project management tools might help you in this step to plan and execute your project, especially for resource management tasks.
While your organization grows, managing projects might become challenging, so you will need the right tools that are capable of enabling your continued growth and scaling with your company.
Step 3 - Roles & responsibilities
Ideally, it’s enough to clearly define roles and responsibilities. Sometimes a simple flow chart or org chart helps to visualize. Alternatively, you can add links to the related SOPs or job descriptions regarding the details of each team member without going into too specific details about roles, responsibilities, and training requirements. Additionally, the objectives section of the quality plan will guide you to define clear roles and responsibilities for the team.
In this step, you should also define how you will communicate with all affected departments and functions, external providers, and customers. When needed, how to resolve problems that may arise between such groups.
Training is also another key pillar under the step: Roles and responsibilities. The competence, and training requirements for each role should be defined.
Identify people within the organization who are responsible for:
- the activities and resources required for the quality plan and ensure that it’s implemented and controlled, and their progress monitored as planned.
- reviewing quality plan inputs, recording these reviews, and resolving conflicts and ambiguities;
- communicating requirements reviewing the results of any audits conducted;
- reviewing and authorizing changes to, or deviations from, the quality plan.
Reporting lines of those involved in implementing the quality plan may be presented in the form of an organizational chart.
Step 4 - QMS and Quality Objectives
In this step, you should define and refer to standards, SOPs, and quality policy specific to your product/project in accordance with your QMS, also define your organization’s quality objectives and KPIs and how you will achieve them. The goal of quality objectives is to:
- Decrease product nonconformities and defects
- Improve product performance
- Increase efficiency
- Ensure the safety of products and processes
- Increase customer satisfaction
Quality objectives can be established based on the quality characteristics of the product/project, and customer requirements or you may consider opportunities for improvement. So they can vary depending on the basis including details on medical device characteristics, uniformity, performance, effectiveness, etc. Furthermore, there are other quality objectives that address cost, utilization, dependability, weight, and many more.
Objectives should be measurable, so you should describe how and when to track each objective. This mechanism ensures the measurement of all quality activities. If a result does not meet the acceptance criteria, you should initiate NCR or CAPA investigations.
To measure and achieve those objectives, you should also define the company audit management process and how to handle CAPA and nonconformities.
Step 5 - Project Inputs
In this step, you will identify the inputs required for the quality plan of your medical device. Additionally, you must define how the project will be controlled and how deliverables will be managed. This includes listing, reviewing, verifying, approving, and distributing documents. You will also need to address any changes to the project scope in accordance with change management procedures."
The project inputs may vary depending on the complexity of your medical device. However, it can be identified based on the following requirements, but not limited to:
- QMS and standard requirements
- Customer requirements
- Regulatory requirements
Industry specifications; - Requirements for and availability of resources
- Requirements of the specific case including technical specifications of the product, if any
- Assessments of risks and opportunities related to the specific case;
- Information on the needs of users of the quality plan;
- Communication requirements
- Other relevant quality plans;
- Any documented information relevant to the quality plan;
Reference these inputs to the quality plan, so it’s easy to identify them when needed.
Bonus - Customer requirements
Here, you can find some of the key activities to identify customers and their needs:
- Identify internal and external customers.
- Discover their needs, expectations, and desires for the product. Also, consider discovering customer feedback.
- Gather all the raw data from the customers.
- Analyze what the customer expects, group, and prioritize their needs:
- Determine methods for identifying product features.
- Select high-level product features and goals.
- Design and develop or improve your product in accordance with customer needs:
- Develop detailed product features and goals.
- Optimize product features and goals.
- Set and publish the final product design.
- Develop the controls/transfer to operations:
- Identify controls needed.
- Design feedback loop.
- Optimize self-control and self-inspection.
- Establish an audit.
- Demonstrate process capability and controllability.
- Plan for transfer to operations.
- Implement the plan and validate the transfer.
- Establish measurements specific to the product.
Step 6 - Document management
In this step, you can outline your document management including methods for controlling documents, identifying changes, and ensuring employees can access current versions of your quality plan. The quality plan is the best place to address required elements of the QMS among the entire product lifecycle including:
- Policies, SOPs, Guidelines, forms
- Records
- Data management
- Internal processes
- Customer satisfaction
- Continuous improvement
- Quality analysis
Step 7 - Project deliverables
In this step, you should define clear guidelines for measurement, monitoring, status reporting, and evaluation for each deliverable and describe the methods for evaluating deliverables against predefined standards or acceptance criteria. Ensure outputs are consistent by establishing and documenting metrics to measure their performance. It is also recommended that inputs and outcomes be reviewed periodically to ensure validity. By measuring and monitoring metrics associated with each process, you can track the project quality plan’s health toward achieving objectives.
Every product should have:
- Quality criteria
- Quality metrics
- Preventive activities
- Quality control activities
- Approval activities
Quality plan template: Step 8! Click here to download the quality plan template for medical devices.
Scilife tips
Quality planning is one of the key elements in quality management. So a well-structured process for quality planning along with good documentation simplifies your quality management processes and streamlines your activities. Furthermore, if you use a robust eQMS system like Scilife, you’ll have a head start when creating a quality plan. Scilife enables you to manage project deliverables and add links to the mentioned documents with one click.
Sometimes there might be a deviation or a change from what was planned. Therefore, when there is a deviation from your quality plan, Scilife helps you to manage your deviation, change, or even nonconformities easily with its built-in features.
Conclusion
Medical device companies grow every day, and naturally, the products, technology, and operations evolve as well. You can imagine that it becomes harder to manage projects when the products and operations are more complex.
It might sound like a lot of work to create well-structured quality planning within your company, adding workload for upper managers as well as managers at lower levels.
Conversely, to be able to compete globally and maintain your position in the market, you should get the most out of the company's assets and resources. Deploying a quality plan allows this to be accomplished.