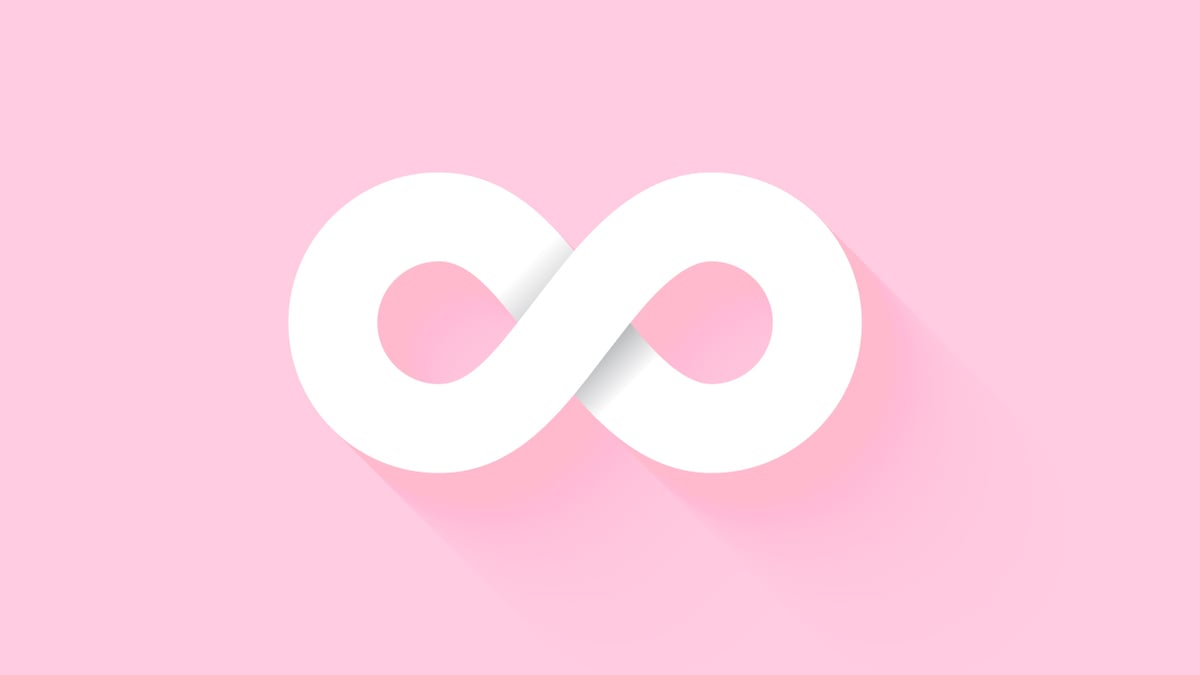
Continuous improvement, the practice of constantly striving to be better, is the goal of modern day self development and countless business philosophies. It’s an interesting goal to embrace too, because by definition perfection can never actually be reached: the point is the pursuit.
"Perfection is not attainable, but if we chase perfection, we can catch excellence"
Vince Lombardi
When it comes to business buzzwords, ‘continuous improvement’ is flung around in plenty of meetings. What does it actually mean, and how does one ‘continually improve’ in practice?
First of all, continuous improvement is not restricted to one industry. The concept of putting strategies into place to get a bit better every day can be applied to pretty much any process within any industry. If we’re talking continuous quality improvement (sometimes abbreviated to CQI), then that’s defined as the process of developing and improving the quality of a business's operations, services, and outputs.
The foundation of continuous quality improvement is teamwork. Suggestions on how and where to improve can originate from any employee in an organization, not just management. In fact, it’s actively encouraged that every single person, no matter their role, analyzes their work and proactively suggests where there's room for improvement. Continuous quality improvement is based on the assumption that problems arise because of changeable factors, not because of the people performing the processes. Factors such as flawed instructions, poorly designed processes, failures of leadership, and so on. As such, continuous quality improvement is supposed to permeate the entirety of an organization - it should become the normal way of doing things for everyone.
So, how does a company put continuous quality improvement into action? Simple in theory, just follow a tried-and-tested methodology! The three best known practices out there are Lean Thinking, Six Sigma and Kaizen. Let’s break each of them down.
Lean Thinking
Sounds like some sort of crazy new diet right? In a way, it sort of is! However, rather than a temporary diet, Lean Thinking is a lifelong transformation of your organization’s way of doing things. The goal of Lean Thinking is exactly as the name of the practice suggests: slimming down operations and cutting out unnecessary activities while preserving or increasing value.
Lean Thinking Cut out unproductive activities |
Lean Thinking originated on the manufacturing floors of car factories. It began with Henry Ford and his disdain for unproductive work. Later, Taiichi Ohno, the father of the Toyota Production System (TPS), became inspired by Ford when optimizing his own car manufacturing processes. In an attempt to cut out ‘wasteful’ activities (which he coined Mudas), Taiichi Ohno decided to implement a strategy for improvement he termed Lean Manufacturing. The simple yet powerful strategy was a roaring success. Lean would take the world by storm, first in car manufacturing but soon in any industry imaginable. Now, lean is commonplace in regulated industries where quality is key as well, including the life sciences.
The Principles of Lean Thinking
The driver of Lean Thinking is customers. In Lean Thinking, value and demand is entirely dictated from the customer’s point of view.
As well as the five Lean Thinking principles depicted above, Lean Thinking is based on these 7 guiding concepts:
-
- Optimize the whole
- Eliminate waste
- Create knowledge
- Build quality in
- Deliver fast by managing flow
- Defer commitment
- Respect people
- Optimize the whole
In terms of continuous quality improvement in the life sciences, ‘waste’ or mudas might include overproduction, overprocessing, transportation, periods of waiting and more. These wasteful activities can be identified and eliminated through many different and very useful tools. For a deep dive into all that, specifically for those in the life sciences, this article is a great start.
In short, Lean Thinking is a fast highway to continuous quality improvement. When done right, you’ll quickly see a huge boost in performance, agility, and efficiency throughout an organization.
Six Sigma
Another way of implementing continuous quality improvement is by using the Six Sigma practice. Invented by a scientist who worked at Motorola in the 1980s, Six Sigma systematically gets rid of inefficiencies and defects (variations) by detecting them through statistical analysis. It’s a methodology that helps make data-driven improvement decisions, rather than relying on guesswork. So, what exactly is Six Sigma, where does this snappy name come from and how can companies use it in continuous quality improvement?
Six Sigma Reduce variation (chance of errors) |
The name Six Sigma is derived from the bell curve used in statistics where one Sigma represents one standard deviation away from the mean. The defect rate is extremely low if the process only shows six of these Sigma’s, three above the mean and three below. That’s because only 3.4 out of a million events along a bell curve would fall outside of six standard deviations. In other words, an error or defect only occurs about three times in a million, statistically speaking!
Apart from reducing variations, Six Sigma has evolved into a more general business-management philosophy, focusing on meeting customer needs, improving customer retention, and generally bettering products and services.
The 5 Principles of Six Sigma
Six Sigma is based on 5 key principles.
- Working for the customer
- Finding problems and focusing on it
- Removing variations and bottlenecks
- Communicating clearly and training teams
- Being flexible and responsive
To implement Six Sigma properly, you should follow a 5-step process called DMAIC.
When combined with Lean Thinking it creates the hybrid concept Lean Six Sigma, a powerful business management strategy that systematically removes waste in addition to reducing variation.
Lean Six Sigma Reduce variation (chance of errors) to statistically insignificant values AND remove unproductive activities through Lean |
Kaizen
Finally it’s time to introduce Kaizen, the darling of continuous improvement! This pratice’s exotic and eloquent name stems from the Japanese words ‘Kai’ (Change) and ‘Zen’ (Good). Yep, you guessed it, Kaizen spells out ‘change for the better’. Kaizen is an approach based on making small, ongoing, and incremental changes to continually improve a process or product.
"Success is the sum of small efforts,
repeated day in and day out."
Robert Collier
The history of Kaizen can be traced back to the time of economic recovery in Japan post-WW2, when Toyota first implemented ‘quality circles’ in its production process. ‘Quality circles’ refer to groups of workers performing the same or similar work, who meet regularly to identify, analyze and solve work-related issues. Business and quality management professionals who visited from America helped influence this new way of doing things. In the 1950s, it became a revolutionary concept in Japan.
Kaizen Change things one small step at a time, but never stop! |
Kaizen was then officially introduced to the Western world in 1986 by Masaaki Imai and made famous through his book ‘Kaizen: The Key to Japan's Competitive Success’. Masaaki dedicated his life to understanding the Kaizen philosophy and even founded the Kaizen Institute. As is the case with the other two continuous improvement practices described earlier, Kaizen is a philosophy and methodology based on several core principles:
The 10 Principles of Kaizen
-
- Improve everything continuously, but remember you can’t improve what you can’t measure.
- Abolish old, traditional ways of doing things.
- Accept no excuses and make things happen.
- Genchi Genbutsu: see it for yourself.
- If something is wrong, correct it, from the root (treat the disease not the symptom).
- Empower everyone to take part in problem-solving.
- Get information and opinions from multiple people.
- Before making decisions, ask "why"-questions five times to get to the root cause. (5 Why Method).
- Be economical. Save money through small improvements to spend the saved money on further improvements.
- Remember that improvement never ends, so never stop trying to improve!
- Improve everything continuously, but remember you can’t improve what you can’t measure.
In practice, Kaizen is implemented through a variety of different tools. For more insights about Kaizen’s practicality in the life sciences, this blog post is a good introduction. In many businesses, Kaizen is used to drive a hyper-focussed development project that addresses a certain issue over a short period of time (2-10 days), known as a ‘Kaizen Event’ (or Kaizen Blitz). A Kaizen Event must have a clearly defined, concise objective and immediately available resources to be able to produce quick breakthrough improvements that fuel team motivation and enthusiasm.
To Sum it Up
Continuous quality improvement can be reached by different roads. Lean Thinking, Six Sigma, Kaizen and their many variations and fusions have stood the test of time and are all solid and excellent practices to implement in any organization striving to improve. When it comes to regulated industries like the life sciences, continuous quality improvement is not only desirable, it’s fundamental in order to meet the constantly evolving demands of the sector.
Now that you know what Lean Thinking, Six Sigma and Kaizen are, it’s time to put that knowledge into action within your own organization, and set off on the long but very rewarding road of continuous improvement!
Discover how a Smart QMS can help you implement these methodologies!