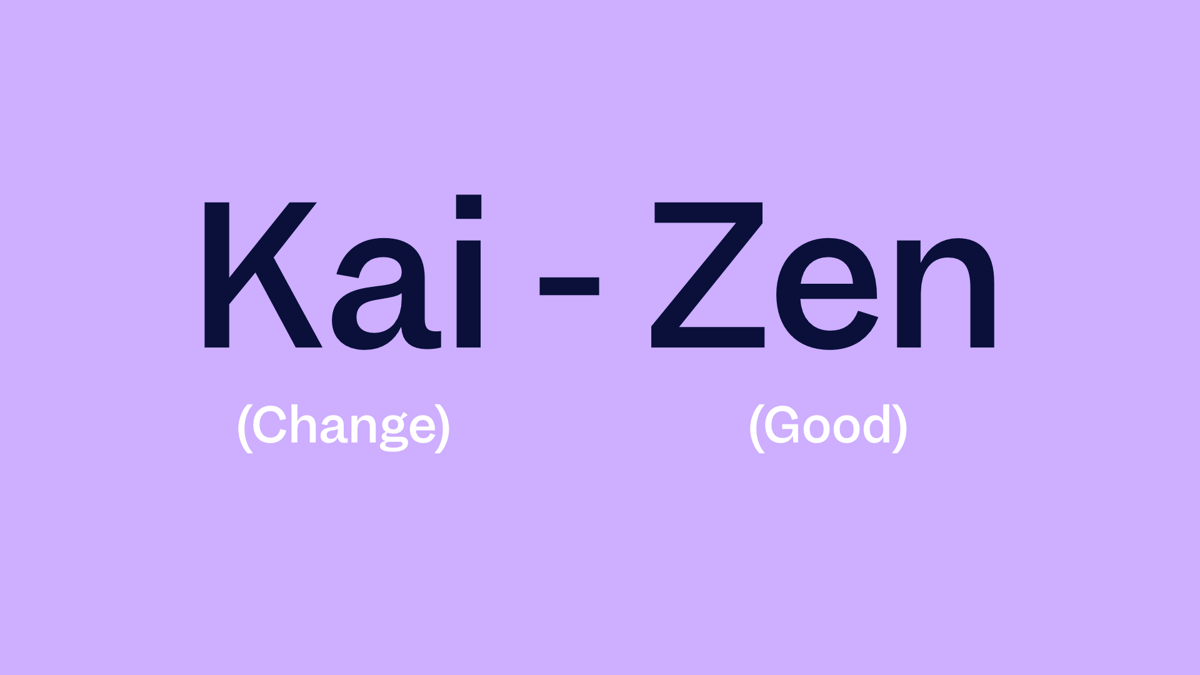
What is Kaizen?
Kaizen is a Japanese term derived from two separate Japanese words, 'Kai' and 'Zen.' The word 'Kai' means change, and 'Zen' means good. Therefore Kaizen literally means 'changing for the good.' Kaizen is a widely accepted philosophy for implementing best practices within organizations. It is an approach that creates a continuous improvement culture through ongoing small incremental changes. In simpler words, Kaizen is the pursuit of doing better than best by challenging the status quo every day. As an outcome, Kaizen creates highly motivated teams that actively participate in building efficient processes.
Before we jump to the main topic, let's get familiar with the Kaizen Principles. The fundamental Kaizen principles that keep the motto of 'changing for the good' alive are as below :
1. Improve everything continuously.
2. Abolish old, traditional concepts.
3. Accept no excuses and make things happen.
4. Say no to the status quo of implementing new methods and assuming how they will work.
5. If something is wrong, correct it.
6. Empower everyone to take part in problem-solving.
7. Get information and opinions from multiple people.
8. Before making decisions, ask "why"-questions five times to get to the root cause. (5 Why Method)
9. Be economical. Save money through small improvements to spend the saved money on further improvements.
10. Remember that improvement has no limits. Never stop trying to improve.
As you can sense now, Kaizen encourages creative thinking in the employees, making the work environment more engaging. As a result, Kaizen can help organizations reap immense benefits in the form of increased innovation and productivity. This article will discuss how Kaizen can form the basis of innovation and improved productivity in the Life Sciences industry.
Kaizen in the Life Sciences
Pharmaceutical, medical device, and biotech companies need to meet stringent regulatory compliances applicable to them. Therefore, it is imperative to demonstrate the ability to meet the quality specifications every single time. Failing to do so means a product may have to be called off from the market, resulting in business loss and loss of patient trust. Life Science companies are in a constant struggle to meet the pricing pressures, demand variability, and higher heterogeneity of customer preferences. That is why life science companies need to keep their employees motivated to do better than the best using optimal resources. Kaizen achieves this through increased employee participation. Employees are constantly analyzing, 'why are we doing what we are doing?' It naturally results in increased awareness among the employees, making them more innovative and creative.
Several life science companies that include big names like Sanofi-Aventis, Boehringer Ingelheim, GlaxoSmithKline, Merck, Dr. Reddy's Laboratory, and Piramal Healthcare have successfully reaped benefits using Kaizen thinking.
Kaizen with Scilife
At Scilife, we know the pressing needs of the life science industry; hence we constantly strive to partner with customers in their Kaizen journey. So how can Kaizen with Scilife make a difference in the life science industry?
Father of Toyota Production System and Japanese industrial engineer Taiichi Ohno has famously said that "Something is wrong if workers do not look around each day, find things that are tedious or boring, and then rewrite the procedures. Even last month's manual should be out of date."
True, isn't it? But does it happen that frequently in the life science industry? The answer is no. This is because compliance with standards like ISO 13485:2016 and ISO 9001: 2015 make the very process of updating manuals (or any Quality Management Document) tedious and boring.
Let's assume that one such company struggling with these issues resolves to use Kaizen for continuous improvement. Now since updating the processes and procedures becomes a bottleneck in becoming a more efficient organization, employees decide to take it up as the first thing to improve.
Then arises the question, 'how will the organization achieve it without violating ISO 13485:2016 and ISO 9001:2015 requisites?' This is where Scilife can pitch in, as it is possible to get this done by adopting Scilife's cloud-based e-QMS system that allows auto versioning, online edits, and approvals. Most importantly, it is also 21 CFR Part 11 compliant. Working with Scilife easily removes the fear of making changes in quality management practices and empowers employees to challenge the status quo more often.
That’s Kaizen: finding more efficient ways of doing things through smart thinking.
Conclusion
In conclusion, Kaizen is not just about improving profit margins. It is about challenging the old traditional approaches to change for the larger good. We as humans love to associate ourselves with a larger purpose and the Kaizen philosophy essentially supports that. The improvement in the profit margin is just a long-lasting byproduct of the excellent work culture that Kaizen creates. Many life science companies have started to question the status quo with Kaizen. These are the companies that are leading by example and creating a role model for success through Kaizen.