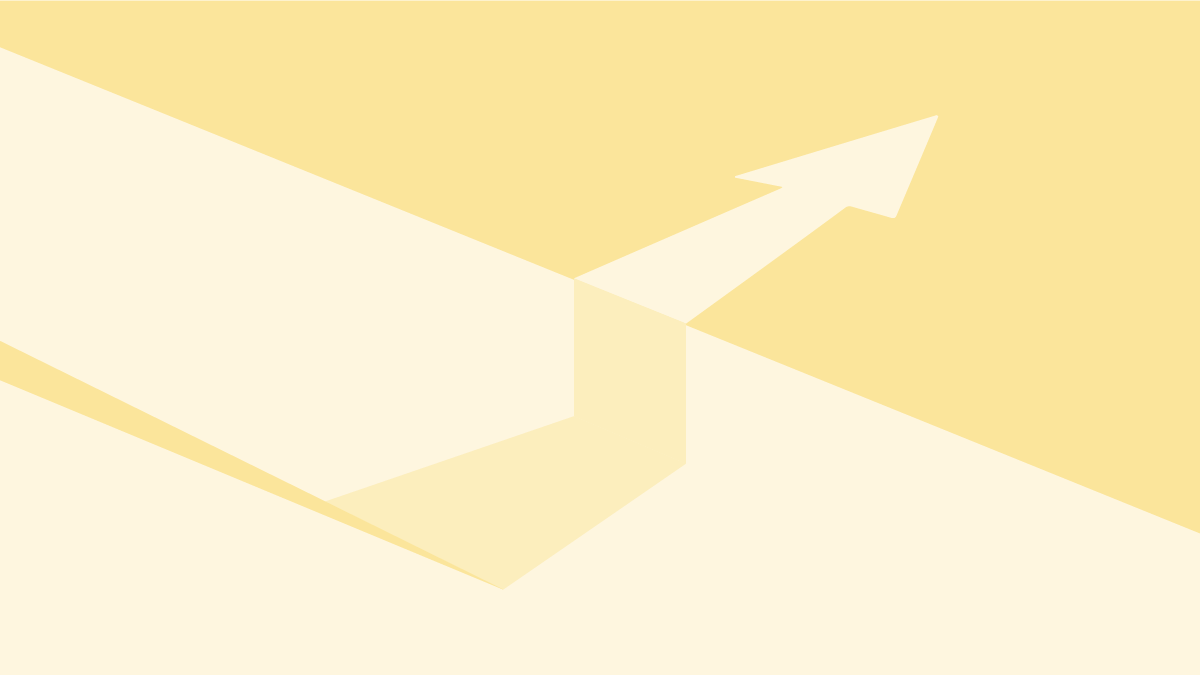
Identify your organization’s needs
On one hand, implementing an eQMS begins with identifying your organization's gaps and challenges through internal audits. Risk assessments and SWOT analysis are also useful. Note that non-compliance issues can result in significant financial and reputational consequences. As a result, it is vital to take proactive steps to mitigate these risks.
The second step is to evaluate the risks associated with non-compliance, wasted resources, data security, data integrity, data loss, and privacy, especially when it comes to confidential information. Assess the potential impact of data breaches and the need for robust security measures.
SWOT analysis is another excellent tool executives can use to identify areas of potential growth, as well as potential weaknesses in Quality Management Systems:
- Strengths might include a skilled and motivated workforce, existing quality management processes that can be improved, and a strong commitment to quality.
- Weaknesses might include excessive use of manual methods, such as the use of Excel spreadsheets to manage quality processes, resistance to change, or outdated legacy systems.
- Opportunities might include improved compliance, faster quality processes, cost reduction, and enhanced data-driven decision-making.
- Threats of remaining in the current state without doing nothing could include loss of opportunity, such as the loss of competitive advantage, or being outdated in technology standards.
To communicate with C-suites effectively, it is essential to use terms they can recognize, such as return on investment, but this term goes beyond cost savings.
What is ROI calculation?
Return on Investment (ROI) calculation is a financial metric used to evaluate the profitability, benefits, and gain of an investment relative to its cost.
Making decisions based on ROI is an essential tool for executives in a variety of business contexts, including the evaluation of investments. ROI helps to measure whether an investment is worthwhile by providing a clear financial picture of how much return is generated from an investment. It also provides an indication of the potential risks associated with the investment.
In the context of an eQMS, ROI calculation helps organizations assess the value and effectiveness of the software in improving the efficiency of quality processes, compliance, and reducing costs.
Here's how you can calculate ROI for eQMS implementation:
- Cost of investment: Identify the costs associated with implementing and maintaining the eQMS system. This includes the initial cost of the software, hardware, implementation, training, and continuous ongoing support over the years. In addition, consider the cost of any additional resources required, such as IT personnel or consultants.
- Calculate net gain from investment: In the case of an eQMS, this refers to the total profit, benefits, and savings realized from the investment. It can take the form of increased revenue, reduced costs, or reduced expenses.
By increasing productivity, for example, and reducing time spent on non-value-added tasks such as searching for paper documentation, training, and audit preparation, direct savings can be realized.
Additionally, analyze the time saved when employees are able to focus on the right task at the right time with fewer reworks, recalls, and manual tasks. These cost savings can be reinvested into other more profitable activities, such as research and development, marketing, or customer service. In addition, increased productivity can also lead to increased customer satisfaction, which eventually results in increased sales and profits.
Try out our ROI Interactive Calculator
At Scilife, we have introduced our new online return on investment value calculator (ROI calculator). It is an interactive tool that provides a detailed breakdown of the savings that our Smart Quality Platform can provide to your business. Use your own information to discover what would be the return on investment with the implementation of an eQMS in your organization:
without Scilife
year with Scilife
Include the following:
(10 cabinets x 200$) + (10 shelves x 150$) = 3500$/year
Include the following:
* Cost of purchasing paper for documentation: 100.000 pages x 0.02$/page = 2000$/year
* Cost of ink/toner and maintenance: 100.000 pages x 0.05$/page = 5000$/year
* Cost of printers and copiers = 3000$/year
Employee time searching for paper documents, assuming 100 employees x 2.5h/week x 52 weeks/year = 130h/year
Saving cost with Scilife
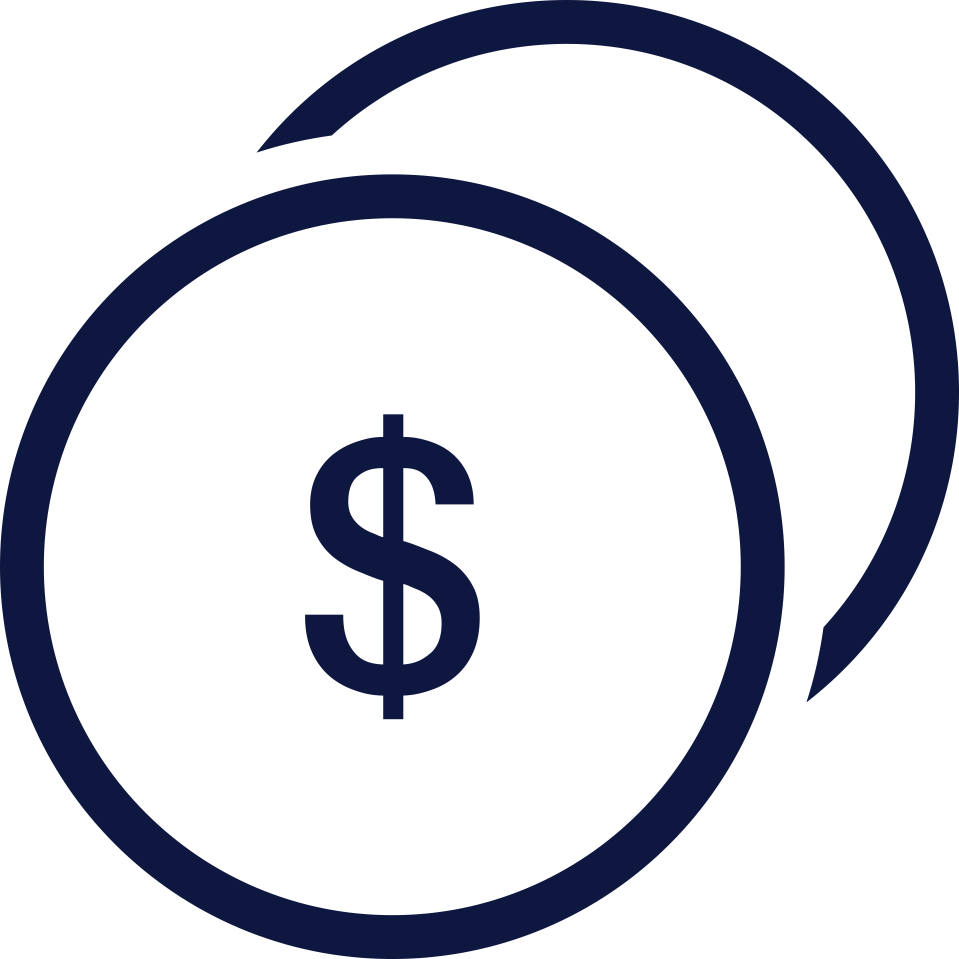
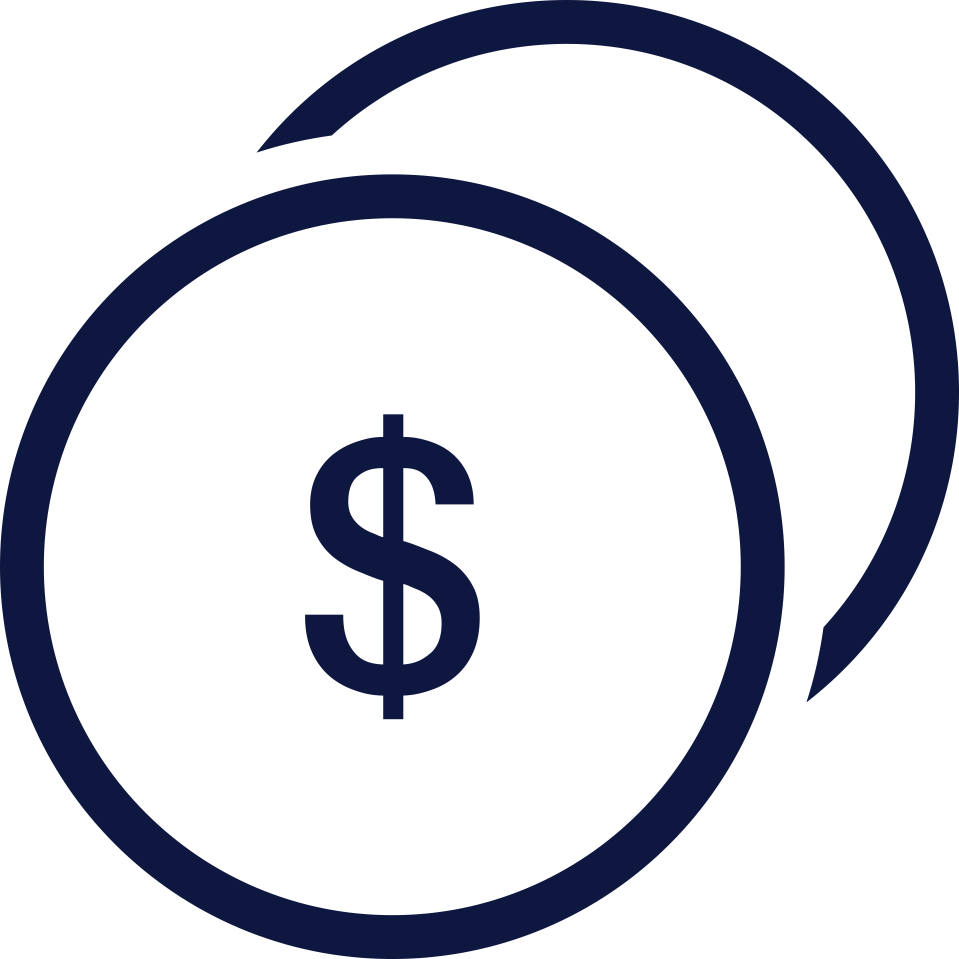
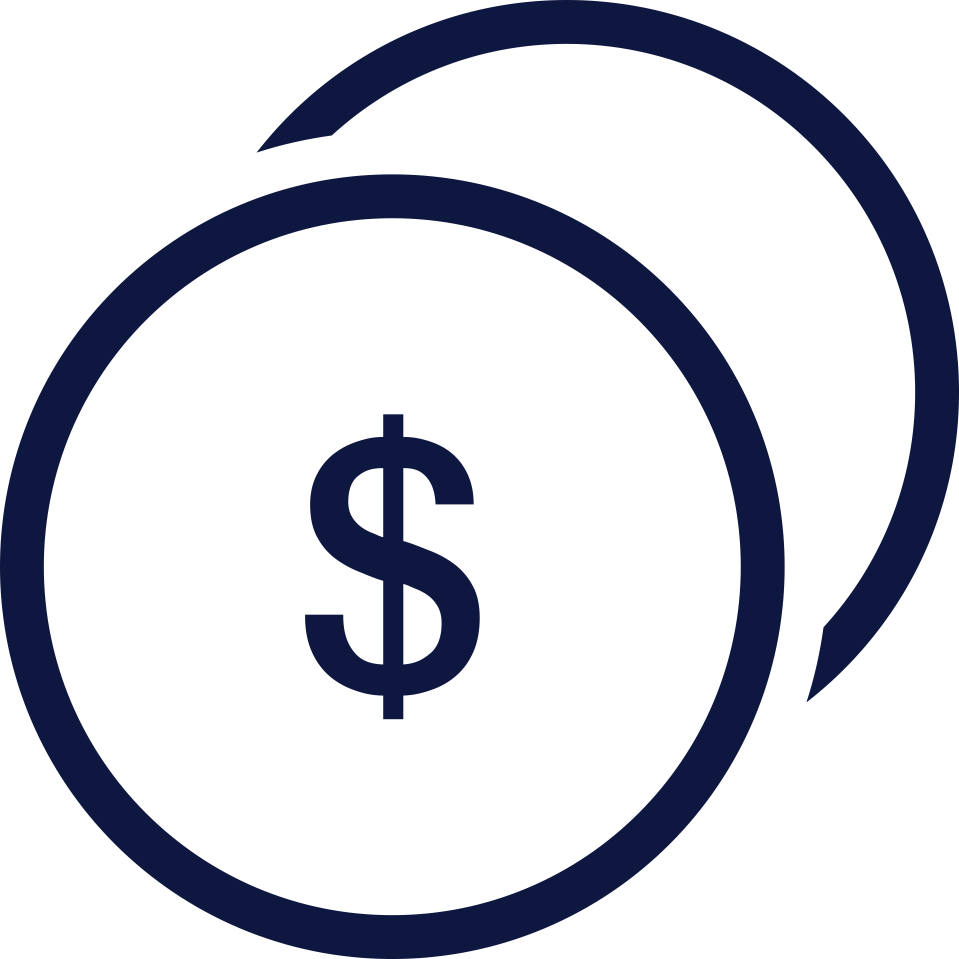
The Benefits of eQMS in Life Sciences
Make use of the following benefits of an eQMS for life sciences to persuade C-suites to consider an eQMS:
Ensured compliance:
With an eQMS, organizations can meet regulatory requirements with less risk and fewer setbacks, while anticipating and generating revenue more rapidly.
Improved document control:
It is cumbersome and error-prone to use legacy systems, such as paper-based documentation. An eQMS centralizes document control, ensuring the latest versions of documents are readily available to authorized personnel, reducing the risk of errors and enhancing overall document management.
Enhanced process efficiency:
By automating a manual QMS, over 40% of the time and resources required to manage new documents will be saved, resulting in greater productivity, efficiency, and accountability.
Real-time decision-making:
By using an eQMS, organizations are able to access data and performance metrics in real-time, allowing them to make better decisions based on the most current, accurate information. By identifying trends, potential areas of improvement, and risks, data-driven decision-making minimizes errors and increases overall performance.
Cost reduction:
Implementing an eQMS eliminates the need for paper printing and manual document control. By eliminating paper, ink, printing, storage, and disposal costs, organizations can significantly reduce their expenses. The ability to access the latest versions of documents and not have to manually enter and review data helps organizations save time and resources.
Enhanced collaboration:
By sharing data, documents, and insights across departments, an eQMS helps teams work more efficiently and effectively, reducing the need for manual processes and errors. Therefore, teams can communicate and collaborate more effectively, leading to faster decisions and resolutions.
ROI use case: A practical example in the pharmaceutical industry
Imagine you are the CEO of a small pharmaceutical industry. Assume the following data:
- Number of employees: 100
- The average salary per employee is $60,000
- The workweek is 40 hours
- The mean hourly rate is $28.9/hour
Based on a 100% paper-based quality management system, consider the following information every year:
- 500 active documents:
- 300 operating procedures (SOPs)
- 100 work instructions (WI)
- 100 other documents (policies, protocols, reports, etc)
- 450 training records (read & understood, and training session)
- 220 quality events:
- 100 deviations
- 100 non-conformities
- 10 complaints per year
- 10 others
Assume the following lead times to complete the lifecycle management, from the edition, review, and approval, to printing, storing, and backup of:
- 5 hours for managing the lifecycle of a document (SOP, WI, and others)
- 0.5 h for tracking, compiling, and reporting a training record
- 5 h for a quality event
Assume these extra costs:
- 100.000 pages are printed every year
- 10 photocopies are rented
- All documentation needs 50m2 space
- Extra external storage space for document custody is rented
- Each employee wastes 2.5 hours per week looking for paper documents in non-added value activities
- Documents are sent to other facilities, suppliers, customers, CMOS, etc by postal mail
- Document storage security and compliance
Here's an extensive analysis of the extra costs of not having an eQMS implemented:
Based on McKinsey's benchmarking data, using an eQMS designed according to Smart Quality principles will increase productivity by the following values:
- 40% productivity increase in document management
- 20% productivity increase in training management
- 40% productivity increase in quality event management
Typically, by increasing productivity, saving resources, boosting release cycle times, improving customer satisfaction, and many other benefits, your quality processes will create and fuel value within your organization, beyond compliance only.
Unlocking Growth: eQMS Adoption Opportunity vs. Hidden Costs of Inaction
A cost of opportunity is the potential benefit of implementing an eQMS, whereas a cost of inaction is the potential loss or penalty that might be incurred if no investment is made.
In addition to calculating ROI, eQMS investments require understanding how to balance the benefits of taking action and the risks of not taking action.
Let's explore both concepts in more detail:
Cost of Opportunity with eQMS: Maximizing Benefits
An eQMS is a catalyst for efficiency, streamlining processes, and accelerating workflows.
This not only boosts productivity but ensures compliance with regulatory standards through automated tracking and document control. Additionally, an eQMS can help reduce costs by automating manual tasks, providing real-time visibility, and helping to identify potential risks before they occur.
By ensuring data integrity and agile adaptability to changes, an eQMS also protects against risks. The software can also help to streamline team communication, improve collaboration and transparency, and improve the quality culture.
Costs of Inaction: Uncovering Hidden Risks
If you do not invest in an eQMS, there are several risks you will have to deal with. One is regulatory noncompliance, which could result in violations and loss of trust and reputation.
In the absence of streamlined processes, operational inefficiencies will persist, hindering productivity and competitiveness.
Data security and integrity might be compromised without the secure framework of an eQMS, exposing the organization to the risks of data breaches.
Additionally, the lack of transparency and traceability can impede continuous improvement efforts.
In essence, the decision to adopt an eQMS is not just about immediate efficiency gains but is a strategic move to proactively mitigate risks and ensure long-term success.
To align the organization's goals with compliance requirements, these factors must be considered.
Conclusion and key takeaways
An eQMS provides a competitive edge for life sciences companies. When embraced properly, an eQMS can reduce costs, streamline operations and improve product quality.
To stay ahead, quality personnel need to prepare a strong case to win executive support. A persuasive argument, backed by a thorough ROI analysis, is key for organizations looking to surpass competitors.
Beyond finances, an eQMS brings advantages like improved compliance and collaboration, making it a strategic investment for efficiency and industry leadership.