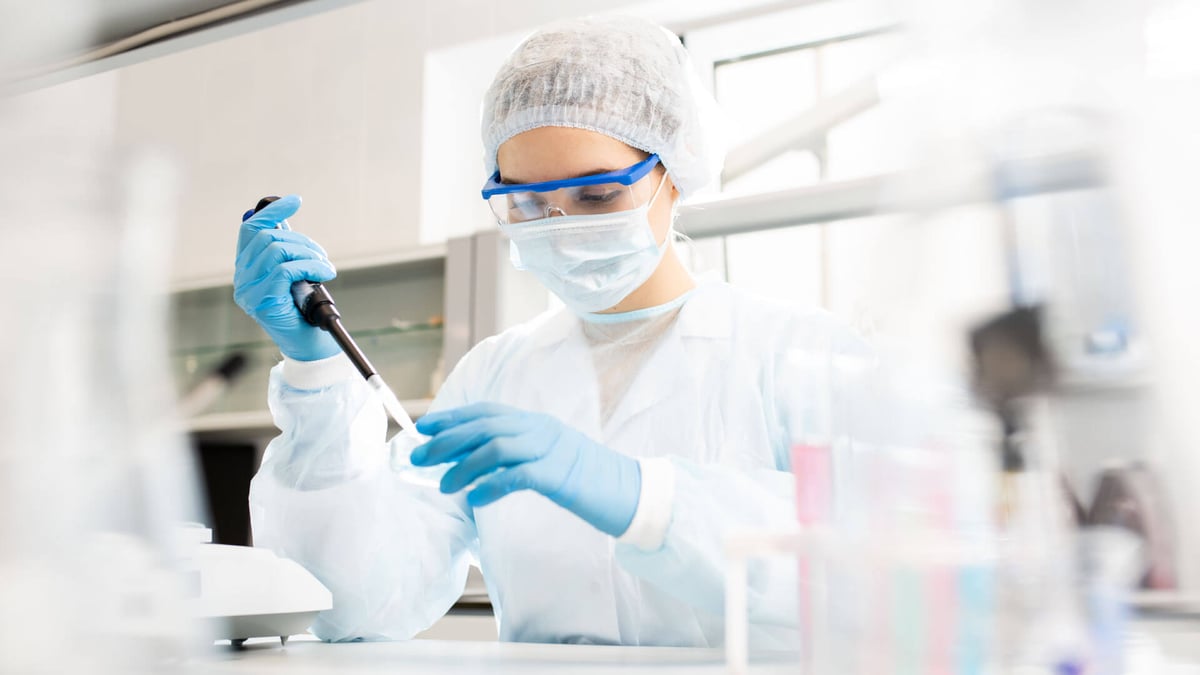
A robust laboratory quality management system is essential in medical research laboratories to ensure the integrity and reliability of the tests conducted. Implementing a laboratory quality management system can be an overwhelming task, but organizations can simplify implementation plans by using an appropriate approach in the Six Sigma philosophy.
The DMADV approach in Six Sigma philosophy is ideal for rolling out a laboratory quality management system. DMADV is an acronym for Define, Measure, Analyze, Design, and Verify, which is a methodology used to design and develop new processes or products. Establishing a quality management system is like creating a new function within your organization, which makes DMADV a suitable approach. This blog post will explore how research laboratories can use the DMADV approach to implement a laboratory quality management system.
Step 1
Define the Scope of the Laboratory Quality Management System
The first step in the DMADV approach is to define the project and its objectives. This includes determining the scope of the laboratory quality management system and identifying the processes and procedures that will be covered by the system. It is crucial to involve all relevant stakeholders, including lab managers, researchers, and quality assurance personnel, to ensure that the laboratory quality management system covers all aspects of the laboratory's operations. This will help to ensure that the laboratory quality management system is appropriate and tailored to the specific needs of the research laboratory. An example of a project charter for the implementation of the Quality Management System can be as follows:
Title: Quality Management System Implementation
Project Manager: [Name]
Start Date: [Date]
End Date: [Date]
Description:
This project aims to implement a laboratory quality management system in the organization to maintain the integrity and reliability of medical research laboratory services. The project will include the development and implementation of processes and procedures to ensure that the laboratory quality management system is effective and efficient. The laboratory quality management system will be based on the ISO 9001:2015, 12 tenets of quality described by the Clinical and Laboratory Standards Institute (CLSI) and ISO 15189 standard and will be tailored to the specific needs of our organization.
Objectives:
-
-
Develop and implement a laboratory quality management system that meets the requirements of the ISO 9001:2015 standard 12 essentials of quality described by the Clinical and Laboratory Standards Institute (CLSI) and ISO 15189 standard.
-
Train all employees on the laboratory quality management system and ensure they understand their roles and responsibilities.
-
Establish a system for monitoring and measuring the effectiveness of the laboratory quality management system.
-
Continuously improve the laboratory quality management system to ensure it remains effective and efficient.
-
Deliverables:
-
-
Laboratory quality management system manual
-
Process flow diagrams
-
Standard operating procedures
-
Training materials and employee training records
-
Reports on laboratory quality management system performance
-
Team:
-
-
Project Manager: [Name]
-
Quality Manager: [Name]
-
Quality Assurance Team: [Names]
-
Subject Matter Experts: [Names]
-
Other key stakeholders: [Names]
-
Timeline:
-
-
Kick-off meeting: [Date]
-
Development of laboratory quality management system manual: [Date]
-
Process flow diagrams: [Date]
-
Standard operating procedures: [Date]
-
Employee training: [Date]
-
Implementation of laboratory quality management system: [Date]
-
Monitoring and measurement: [Date]
-
Continuous improvement: [Date]
-
Budget: [Budget]
Risks:
-
-
Lack of employee buy-in and engagement
-
Difficulty in integrating the laboratory quality management system with existing systems and processes
-
Inadequate resources (time, money, personnel)
-
Resistance to change
-
Approval: [Name and Signature of Project Sponsor and/or Steering Committee]
Step 2
Measure the Key Performance Indicators (KPIs) for the Laboratory Quality Management System
Since our objective is to implement a Quality Management System that complies with ISO 15189 and the Clinical and Laboratory Standards Institute (CLSI), it must be evaluated for 12 essentials. Therefore research laboratories should develop SMART KPIs for assessing the laboratory quality management system. SMART KPIs are specific, measurable, achievable, relevant, and time-bound targets used to evaluate an organization's performance. In the context of the 12 essentials of quality in ISO 15189, SMART KPIs can be used to assess the performance of a medical laboratory concerning each of the 12 essentials.
Here are examples of SMART KPIs for each of the 12 essentials of quality in ISO 15189:
1. Organization:
Expectation: Measure the existence of quality-driven culture in the organization.
KPI: Percentage of quality management reviews conducted on schedule in the last year.
2. Personnel:
Expectation: Measure the qualified staff members in the research laboratory.
KPI: Percentage of staff that have current certifications. Percentage of staff that have received relevant training within the last year.
3. Equipment:
Expectation: Measure the qualified and calibrated equipment in the research laboratory.
KPI: Percentage of equipment calibrated on schedule in the last year.
4. Purchasing and Inventory:
Expectation: Measure the qualified vendors for the research laboratory.
KPI: Percentage of suppliers that have qualified supplier audit in the last year.
5. Process Control:
Expectation: Measure the effectiveness of process controls within the research laboratory.
KPI: Percentage of quality control results that fall within the acceptable range in the last year.
6. Information Management:
Expectation: Measure the information accuracy, security, confidentiality, and accessibility to individuals with the correct privileges
KPI: Percentage of information that deviates from the 21 CFR Part 11 compliance requirements in the last year.
7. Documents and Records:
Expectation: Measure the documents and records accuracy, security, confidentiality, and accessibility to individuals with the correct privileges
KPI: The percentage of documents and records that deviate from the 21 CFR Part 11 compliance requirements in the last year.
8. Occurrence Management:
Expectation: Measure non-conformance occurrence.
KPI: Percentage of non-conformance occurrences during audits in the last year.
9. Assessment:
Expectation: Measure the performance against internal or external benchmarks.
KPI: Percentage of non-conformance occurrences compared to the last year's industrial standard.
10. Process Improvement:
Expectation: Measure adherence to continuous improvement practices.
KPI: Percentage of increase in CAPAs in the last year.
11. Customer Service:
Expectation: Measure the customer experience.
KPI: Percentage of customer complaints resolved within a specified time frame in the last year.
12. Facilities and Safety:
Expectation: Measure the research laboratory's safety, security, and cleanliness.
KPI: Percentage of Safety incident occurrences in the last year.
These are just examples, and it is essential to note that the KPIs may vary depending on the size and complexity of the lab and the specific requirements of the lab.
Step 3
Analyze the Possible Hurdles in Implementing the Quality Management System
The third step is to analyze the KPIs collected in the previous step to identify areas for improvement. This includes identifying the root causes of problems and determining the potential impact of the problems on the research laboratory's operations. Again, involving all relevant stakeholders in this process is essential to ensure that the issues identified are addressed comprehensively and effectively.
Step 4
Design the Quality Management System
The fourth step is to design the new processes and procedures that will be implemented as part of the laboratory quality management system. This includes developing detailed standard operating procedures for implementing the laboratory quality management system, including procedures for monitoring and measuring the research laboratory's performance, as well as procedures for identifying and correcting problems. As before, it is important to involve all relevant stakeholders in this process to ensure that the procedures are appropriate and achievable.
Step 5
Verify Conformance to the Quality Management System
The final step is to verify that the new processes and procedures are working effectively. This includes testing the new procedures in a controlled environment and monitoring the laboratory's KPIs to ensure that the quality standards are being met. It is important to establish a system for monitoring the laboratory's KPIs, including procedures for identifying and correcting problems. This will help to ensure that the laboratory quality management system is effective and that the laboratory's operations are of the highest quality.
Conclusion
Implementing a quality management system in a research laboratory is essential to ensure the integrity and reliability of the research conducted in the lab. By using the DMADV approach, research laboratories can establish a robust laboratory quality management system that will improve the quality of their operations. The DMADV approach is a structured process that helps to ensure that the laboratory quality management system is appropriate, effective, and tailored to the specific needs of the laboratory. By following the steps outlined in this blog post, research laboratories can implement a laboratory quality management system that will help to ensure the integrity and reliability of the research they conduct.