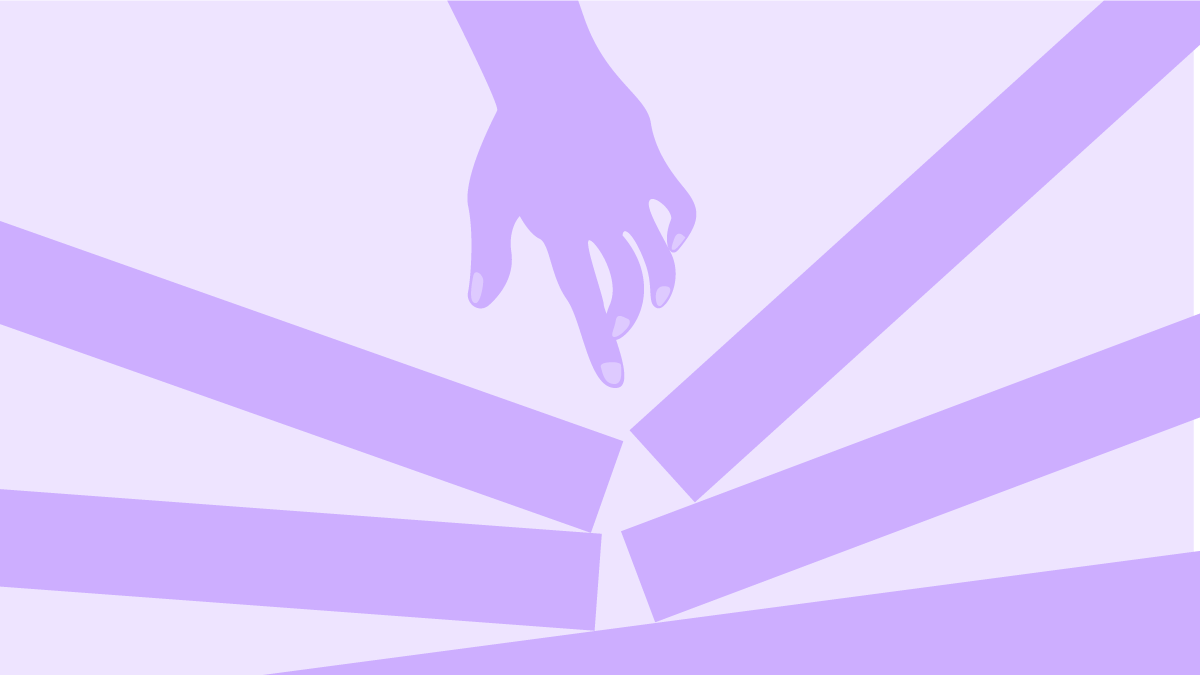
Root Cause Analysis (RCA) is a systematic process used to identify the underlying cause or causes that lead to a problem or incident, with the goal of preventing its recurrence in the future. It is a systematic approach employed in various industries, including the life sciences. The purpose is to understand the fundamental reason(s) behind an issue, rather than just addressing its symptoms. RCA aims to identify what, how, and why an event occurred, allowing organizations to implement effective corrective and preventive actions.
In the life sciences industry, RCA is used for reporting and investigating product defects, process failures, compliance failures, adverse events, patient safety issues, clinical trial failures, etc..
The responsible stakeholders involved in the investigation of the concerned defect or failure often assemble in the form of a cross-functional team and assign probable root causes for the failure or defect through a brainstorming session. For clarity, root cause analysis is often performed with the help of tools such as the Ishikawa Diagram (Fishbone diagram), Five Whys Technique, Failure Mode Effect Analysis, Fault Tree Analysis, and Risk Ranking.
Is human error really a root cause?
Citing human error as a root cause is the easiest way to ignore underlying issues and unfortunately, it happens more often than it should. For example, while using the Ishikawa Diagram for the RCA, the team classifies all the probable root causes into the 5M categories as a starting point. These categories are often labeled as Manpower, Material, Method, Machine, Measurement, and Miscellaneous causes. Out of these five categories, the Manpower related root causes are the most debated ones as regrettably, this category is exploited as a scapegoat under the label of ‘human error’.
The same can be true for other RCA techniques when the team lands on a probable root cause as ‘human error’ during the investigation process.
Landing on a human error as the root cause too often is undesirable as it starts a never-ending passing-the-buck game that spoils your company’s quality culture, and at worst, the real issues remain unaddressed resulting in multiple recurrences. Therefore, in this article we will discuss how to handle a recurring failure that is often attributed to human error, knowing that human error can not really be a root cause.
Do you want to dive deeper into the Root Cause Analysis topic?
Watch our training below!
What is behind human error?
The process of RCA involves running your train of thought until you have no further questions to ask. Your train of thought should only stop when you see a direct correlation with the problem. Often when you label an issue as ‘human error’ you may still have some difficult questions unanswered. If you think deeper these issues will point toward your systemic flaws.
Let’s take a simple example of parallax error that occurs when two different scientists try to measure the volume of a liquid using a measuring cylinder. The error could potentially occur because one scientist measured the volume by observing the lower meniscus while the other did it by measuring the upper meniscus. It could be tempting to label the error as ‘human error’ but in reality, there could be systemic issues such as the inexistence of a standard operating procedure that describes which meniscus should be measured for the specific liquid.
In FDA-regulated manufacturing, you are not only expected to point towards causes but also eliminate them through proper Corrective and Preventive Actions. If you label the issue as ‘human error’ and do nothing about it, then you deny the possibility of improving your quality management system. Having an issue that is frequently labeled as ‘human error’ indicates that your quality management is person-dependent and not system-dependent. Such systemic flaws may be the hidden culprits in many FDA-regulated scenarios.
It’s time we unveil these masked issues using cognitive psychology models and build robust quality management systems to handle the real issues behind human error.
A model for analyzing Human Error
It is essential to objectively investigate the causes labeled as human error using human factors engineering and cognitive psychology models such as the Skills, Rules, Knowledge (SRK) framework. It is used to understand how people perform tasks and make conclusive decisions. Let’s understand each term in the SRK framework and the cognitive processes involved in decision-making:
Skills (S):
Definition:
Skills refer to actions that are performed automatically and without conscious thought. These are tasks that have been practiced to the point where they become almost instinctive.
Example:
Skills could include basic laboratory techniques, pipetting accurately, or using specific software for data analysis. These tasks have been practiced to the point where they can be done efficiently without much cognitive effort.
Rules (R):
Definition:
Rules are decision-making processes based on explicit guidelines or protocols. When a situation is recognized, specific rules are applied to determine the appropriate action.
Example:
Life sciences professionals often follow predefined standard operating procedures, work instructions, and regulatory guidelines when conducting experiments or analyzing data. These rules help in making accurate decisions in various situations.
Knowledge (K):
Definition:
Knowledge represents understanding and problem-solving ability. It involves the application of general principles and strategies to solve new or unfamiliar problems.
Example:
Life sciences employees rely on their knowledge of biological processes, experimental design, and statistical methods to solve complex research problems. This knowledge is beyond following established protocols (rules) or performing routine tasks (skills) but also about understanding the underlying principles and adapting to unique situations.
The SRK model helps us understand the cognitive processes involved in the decision-making process. Once we know the cognitive processes that lead to human errors, we can make improvements in the decision-making process using a Generic Error Modeling System (GEMS) as follows:
- Definition: GEMS is a framework used to identify and analyze human errors in complex systems. It categorizes errors based on cognitive processes, helping professionals understand how and why errors occur.
- Application: GEMS can be used to analyze errors made during experiments, data analysis, or interpretation of results. By understanding the cognitive processes behind errors (such as misapplying rules or misunderstanding underlying knowledge), organizations can implement strategies to minimize the likelihood of these errors occurring in the future.
In this manner, the integration of the SRK framework and the Generic Error Modeling System (GEMS) further allows for a systematic analysis of errors, leading to improvements in processes and reducing the likelihood of future mistakes.
What can we do to avoid it?
Now that we have understood the SRK and GEMS framework, let’s find out what could be an appropriate action plan under different circumstances. According to our understanding of the cognitive root cause, we can implement different problem-solving strategies. Below are a few examples:
- Skill-based errors often occur due to momentary inattention or temporary memory loss, leading to slips or lapses. By addressing distractions and improving focus, we can reduce these errors.
- Knowledge-based errors arise when individuals are overwhelmed by multitasking or lacking focus. To mitigate these errors, we need to ask: Why is multitasking happening? Are the departments under-resourced? Is there a lack of awareness of an individual’s workload?
- Rule-based errors often result from misapplication of rules or procedures. To address these, it’s crucial to ensure adequate training and detailed, clear standard operating procedures (SOPs). If training falls short, we must examine why it’s failing to prepare individuals for their tasks.
- Systemic issues in documentation can also contribute to errors. Streamlining documentation processes, ensuring up-to-date SOPs, and making them easily accessible can significantly reduce errors.
Conclusion
The idea is to build a quality culture by creating an effective Corrective and Preventive Action Plan rather than avoiding it and digging deeper into the problem and identifying a superficial root cause with no Corrective and Preventive Actions. Most importantly, labeling the root cause as ‘human error’ doesn’t put an end to the story, it is where the story begins. Our responsibility is to create a robust system that doesn’t let ‘human error’ occur in the first place.
We’ve all had those moments when human error threw a wrench in the works. Share your story and the lessons you’ve learned!