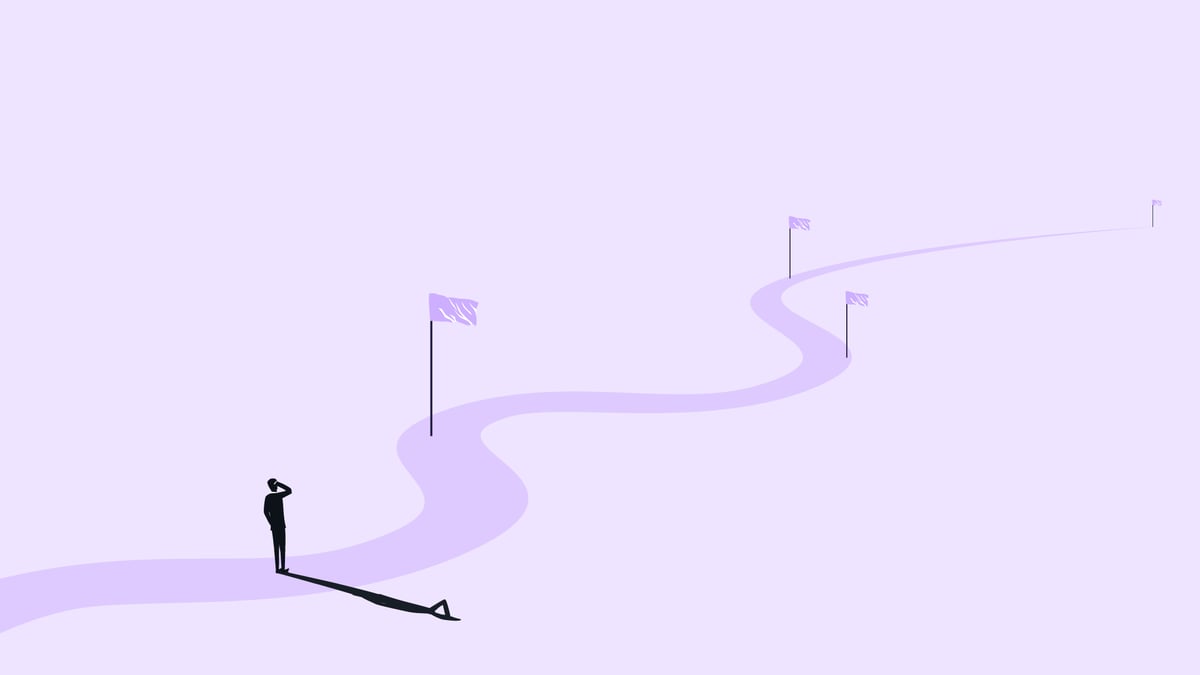
What Is a Non-Conformance Report?
A non-conformance report is a document that explains a deviation from the anticipated outcome of a process or product. Some examples of events in the Life Sciences that may call for a non-conformance report are:
- Process non-conformance:
- Sterile environment not maintained.
- A bug in the peak area calculation feature of chromatography software.
- Product non-conformance:
- Unclear embossing on a tablet.
- Discolored product.
- A medical device has more than the specified variation in heart rate measurement.
These issues are associated with serious patient risks, so addressing them should be a high priority. Such non-conformities are addressed with the help of a non-conformance report. Typically, a non-compliance report contains information on:
- The nature of the deviation: What exactly went wrong? What are the consequences?
- The root cause: Why exactly has it gone wrong?
- Corrective and preventive action plans (CAPAs) to avoid the issue in the future.
A good Quality Manager knows that non-conformance is part and parcel of everyday manufacturing activities in the life sciences industry. There are so many changes happening in the real world, it is almost impossible not to have a non-conformance. A good Quality Manager always prefers to write a non-conformance over ignoring or not-reporting a non-conformance! This article will discuss why a non-conformance report is important and how to write a crisp and clear non-conformance report.
Why Is a Non-Conformance Report Critical?
The statutory requirement is one of the most important reasons for writing a non-conformance report. For example, the US FDA recommends having a process in place to address nonconformances. Furthermore, the FDA states that this process must include steps for identifying the problem, controlling the affected product, taking action, and reworking the policies and procedures that caused the problem in the first place. FDA 21 CFR Part 820.90 suggests three components to address a nonconformance:
- Control of the non-conforming product,
- Review and disposition of the nonconforming product, and
- Rework policy and procedure.
Similarly, the quality system regulation for medical devices stipulates having procedures for the identification, documentation, evaluation, segregation, and disposition of nonconforming products. ISO 13485:2016 – 8.3.4 and ISO 9001: 2015 guidelines also reiterate the statutory requirements of the FDA.
In addition to being a statutory requirement, every non-conformance report is associated with certain risks and opportunities. The risks associated with not having a non-conformity report are:
- Not reporting non-conformance results in hidden factories.
- The hidden factories decrease the quality and efficiency of the operation.
- The decreased quality of product or process may also result in market reputation loss.
- A market complaint received against non-conformance can result in a serious statutory compliance issue.
- The manufacturer may incur losses if a statutory callback is needed for released batches.
- Statutory non-compliance can result in a fine and/or ban in the respective market.
- A non-conformance gone unreported can be discovered during regulatory audits resulting in non-compliance observations.
- Every unreported non-conformance is a lost opportunity for improvement.
Now, let’s look at the positive side of non-conformance – the opportunities associated with a non-conformance report:
- Non-conformity reporting does not allow hidden factories to accumulate.
- Non-conformance reporting acknowledges an area for improvement and allows the team to identify the root cause for defining a corrective and preventive action plan.
- This results in improved product quality and process efficiency.
- It helps maintain the market reputation of the brand.
- It avoids non-compliance observations in regulatory audits.
- It builds a sustainable product and process.
- All of this helps increase long-term profits by avoiding a loss of business.
It is therefore obvious that it is very important to acknowledge any non-conformance and draft a non-conformance report to turn all the above-mentioned risks into opportunities.
8 Steps to a Crisp and Clear
Non-Conformance Report
Step 1: Address the What
Keep it simple! Addressing too many concerns in a single non-conformance report can complicate things. Therefore, write one non-conformance report per issue. Be precise when mentioning what exactly has gone wrong. Limit the scope of the non-conformance report to the sole issue it pertains to.
Step 2: Address the When
Mention the occurrence date and time when the occurrence was first observed.
Step 3: Address the Who
Mention the names of the stakeholders who were present at the time of the non-conformance. This may include stakeholders directly involved in the execution of events and those responsible for managing the execution.
Step 4: Locate the Where
Mention the location of the occurring non-conformance where it was first observed.
Step 5: Address the Why
The root cause analysis is the heart of the non-conformance report. Therefore, addressing the why correctly is crucial to your non-conformance report. There are several methods that can be used to address the why effectively, but the most popular ones are the 5 Whys and the Ishikawa Diagram.
The 5 Whys
In the 5 Whys technique, a facilitator assembles the team of responsible stakeholders (the Whos) and asks them reasonable Why questions. Typically, the first Why question is “Why did the non-conformance occur?” When the team members answer the question, the facilitator asks the next question: “Why did that reason itself occur?” This way, the facilitator continues to ask a series of questions which ultimately helps the team arrive at the root cause. Depending on the complexity, it may take more than five Why questions to arrive at the root cause. An example of the 5 Why technique applied to a non-conformance of traffic rules is illustrated in the following graphic.
The Ishikawa Diagram
The Ishikawa Diagram is often referred to as Fishbone Diagram, Herringbone Diagram, Cause-and-Effect Diagram, or Fishikawa Diagram. Named after its creator Kaoru Ishikawa, the diagram shows the potential causes of a specific event. Resembling a fish skeleton, the “ribs” represent the causes of an event with the final outcome appearing at the head of the skeleton. In a typical manufacturing scenario, the causes (“ribs”) are grouped under the categories of Manpower, Material, Machine, Method, Measurement, and Miscellaneous (or Mother Nature), as shown in the illustration below.
Step 6: Work on the Hows
Now that you know the exact reason for the non-conformance occurrence, it is time to work on how to avoid future occurrences. Writing down CAPAs can help do this effectively. The corrective actions in the CAPAs relate to mitigating the events, whereas the preventive actions relate to implementing robust processes for avoiding future occurrences of the non-conformance.
Generally speaking, we all know that prevention is better than cure, but when the damage is already done, a cure may be needed in the form of corrective actions. Some of the most common corrective actions here are:
-
- Control the non-conformance:
This is an immediate step that needs to be taken as soon as the non-conformance is discovered. How you control this may depend on the processing stage of the product:
- Control the non-conformance:
-
-
- If the product has already been shipped to the market, you may need a product callback from the market.
- If the non-conformance relates to one of the in-process stages of the product, then all non-conforming processes should be halted until the root cause of the nonconformance is identified and addressed.
- If a product or its parts are impacted, these need to be controlled as the nonconforming product or parts.
- Typically, the nonconforming product is controlled in a ‘Hold Area’ by the Quality Control Department. Controlling the non-conforming product or process gives you time for a proper root cause assessment of the non-conformance to take decisive actions.
- Determine the disposition actions:
There could be several disposition actions you can take depending on the product stage and the extent of damage to the product quality. Some of these actions are:
-
-
-
- If the product poses very high risks to patient health or becomes unprocessable, your team may need to scrap the product.
- If the non-conformance occurs because of faulty shipments from the supplier, then your team may decide to return the faulty shipments to the supplier.
- If a problem is found with a new version of the medical device or software as a medical device, your team may consider downgrading the product to the last bug-free version.
- Your team can also decide to do nothing and use the product as-is, assuming the severity of the effect on patient health is negligible. For example, the severity can be negligible when the product's flaw is merely aesthetic.
- If the product fails in an in-process step, your team may decide to reprocess the in-process product to meet the desired specifications.
-
After you have taken corrective actions on an immediate basis, you may want to involve your continuous improvement team to eliminate the root cause. An action plan to eliminate the root cause is nothing but a preventive action plan.
Step 7: Follow the Principles of Data Integrity
The non-conformance report is an auditable document. Therefore, it must meet the data integrity requirements applicable to all regulatory documents. One of the simplest ways to do so is by following ALCOA+ and making the non-conformance report attributable, legible, contemporaneous, original, accurate, complete, consistent, enduring, and available. A software solution like Scilife is going to help you by leaps and bounds here.
Step 8: Monitor the Effectiveness of CAPAs
Last but not least, monitor the effectiveness of the CAPAs and look out for a recurrence of the non-conformance. If your root cause analysis was incorrect, non-conformance will likely recur. If it does, you might need to go back to Step 5 and redo the root cause analysis to explore other reasons that might have caused the non-conformance.
Conclusion
In a nutshell, processes that deliver perfect products don’t really exist in the real world. That is why non-conformance reporting should not be considered taboo. Unaddressed non-conformities can otherwise work like a boomerang and come back to smack you in the head in the form of product recalls, legal penalties, and potential patient harm. Therefore, a good Quality Manager does not avoid writing a non-conformance report. Instead, a successful Quality Manager knows that a non-conformance report can simultaneously improve the product quality and boost the business's sustainability. The 5Ws1H strategy and ALCOA+ principles we discussed can become your key tools for writing a better non-conformity report.
Do you know you can automate the full process, from detecting the deviation to creating the final CAPAs? Discover how with Scilife!