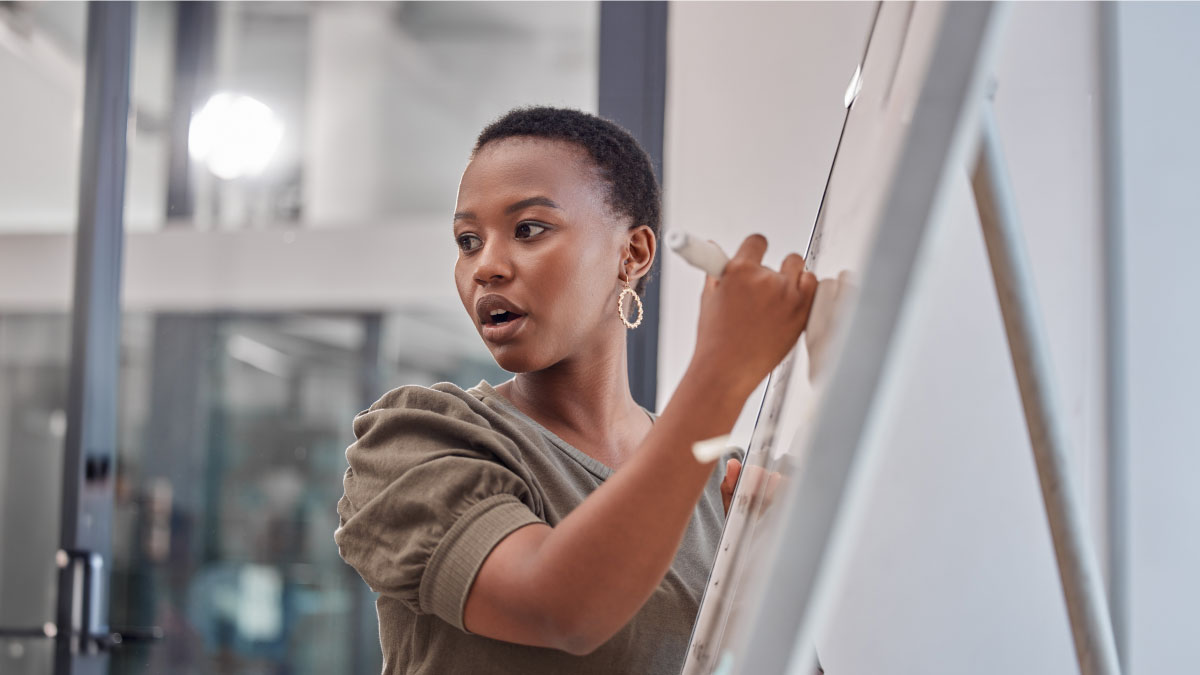
In many countries, including the USA, employee competence is a regulatory requirement for the manufacturing and sale of Life Sciences products. The term ‘competence’ refers to the relevance and frequency with which a skill is practiced. It also refers to the dexterity with which a skill is practiced.
Let’s take a look at an FDA citation issued for the manufacturer Apollo Care to better understand this term in practice:
“Your firm failed to ensure that each person engaged in the manufacture, processing, packing, or holding of a drug product has the education, training, and experience, or any combination thereof, to enable that person to perform his or her assigned functions (21 CFR 211.25(a)).”
This means that the FDA is not only looking for the staff’s mere educational qualifications but cares about the combination of education, training, and experience to perform assigned functions to a staff member. It also highlights that the term ‘qualification’ is often misconstrued as competence. Qualification solely indicates the eligibility of someone to do something, whereas competence represents the ability of the individual to do something successfully and efficiently. In other words, competence goes one step beyond qualification.
That is why several regulations and certification bodies use employee competence as an indirect measure of the ability to deliver Quality products and services consistently.
Therefore, employee competence can be stated as observable and measurable knowledge, education, training, experience, skills, abilities, and personal attributes that contribute to enhanced employee performance. Ultimately, employee competence results in organizational success. Let’s deep dive into the importance of employee competence and how it can help your organization foster a Quality culture.
Why Does Employee Competence Matter?
There are five key reasons that show how important employee competence in the Life Sciences is. Let’s look at them one by one.
Regulatory Compliance
First and foremost, a warning letter regarding a non-compliance issue is the last thing any healthcare manufacturer likes to receive from the US FDA. This makes regulatory compliance so important, it is the first key reason why employee competence matters. Both ISO 9001:2015 and 21 CFR Part 211.25 outline essential guidelines and regulations for meeting employee competence requirements respectively. We will dig into this further in later parts of the present article.
Quality Culture
The second reason for employee competence is its inseparable association with the organization’s Quality culture. The efficient management of employee competence demonstrates an organization’s commitment towards engaging well-trained and skilled staff to deliver the most appropriate job responsibilities. When employees are assigned job responsibilities according to their qualifications, knowledge, experience, and skills, the chances of QMS deviations reduce naturally. As a byproduct of reduced deviations, you will be able to foster a Quality culture in your organization.
People Management
The third reason for employee competence is efficient people management (also known as the HR department). Employee competence records can help employees and managers alike with career planning by enabling them to quickly understand employee skill gaps. At the same time, managers can work out alternate career progression paths and additional responsibilities for the employees based on their competencies.
Health and Safety
The fourth reason in favor of employee competence is health and safety. This is because competence is not only an essential indicator of the ability of a manufacturer to deliver Quality products and services but also a major of the ‘Health and Safety’ awareness with which the manufacturer will be able to deliver the products and service.
Customer Trust
The fifth and final reason for employee competence is customer trust. Employee competence helps tremendously in earning customer trust. There is hardly any business that can sustain itself without loyal customers who trust the products of the manufacturer or the services they offer.
What Are Employee Competence Regulations?
There are five key reasons that show how important employee competence in the Life Sciences is. Let’s look at them one by one.
ISO 9001:2015
The compliance of ISO 9001:2015 is centered around the famous mantra of “Do what you say, and say what you do.” This sounds very simple at first; however, in practice, the service or product providers inadvertently make overstatements about the actions, features, and Quality to the potential customers. ISO 9001 tries to keep a countercheck on these overstatements by ensuring that the employees involved in doing the work have the necessary competence to plan, do, check, and act on the deliverables assigned to them. The purpose is to ensure that the employees know what is expected from them and deliver what the organization promises to its customers.
Section 7.2 of ISO 9001:2015(E) requires the organization to:
- Determine the necessary competence of person(s) doing work under its control that affects the performance and effectiveness of the Quality management system;
- Ensure that these persons are competent on the basis of appropriate education, training, or experience; and
- Where applicable, take actions to acquire the necessary competence, and evaluate the effectiveness of the actions taken.
21 CFR 211.25
The Code of Federal Regulations (commonly abbreviated as CFR) is the bible of every healthcare manufacturer, be it a drug manufacturer, drug product manufacturer, or biomedical device manufacturer. The federal regulation also ensures a check on the competence level of the workforce engaged in manufacturing healthcare products. Section 211.25(a) states that:
- Each person engaged in the manufacture, processing, packing, or holding of a drug product shall have education, training, and experience, or any combination thereof, to enable that person to perform the assigned functions. Training shall be in the particular operations that the employee performs and in current good manufacturing practices (including the current good manufacturing practice regulations in this chapter and written procedures required by these regulations) as they relate to the employee’s functions. Training in current good manufacturing practices shall be conducted by qualified individuals on a continuing basis and with sufficient frequency to ensure that employees remain familiar with CGMP requirements applicable to them.
- Each person responsible for supervising the manufacture, processing, packing, or holding of a drug product shall have the education, training, and experience, or any combination thereof, to perform assigned functions in such a manner as to provide assurance that the drug product has the safety, identity, strength, Quality, and purity that it purports or is represented to possess.
- There shall be an adequate number of qualified personnel to perform and supervise the manufacture, processing, packing, or holding of each drug product.
The FDA has been actively citing observations related to competence in its audits. The trending number of such citations under Section 211.25(a) is shown here:
The summary of all the citations under Section 211.25 for the year 2022 is sourced from the FDA website and presented below:
How eQMS and Smart Quality Connect to Employee Competence
The eQMS solutions and Smart Quality approach towards QMS can help you keep track of your employee competence in real-time. Scilife’s employee competence management solution can digitally transform the record-keeping process for you. The Smart Quality approach helps you connect the dots between employee training, employee competence, and employee performance.
If you use an eQMS solution, the responsibility of updating the competencies is shifted to each employee. Employees can use their login credentials to access the competence management solution and update their latest competencies along with necessary certifications. The information entered by each employee is duly reviewed and approved by Quality Assurance (QA). The solution makes your QA’s life easier while ensuring 100% compliance with regulatory requirements. When an employee fails to meet their key competencies, QA can identify the training gaps and impart the necessary training to the employee.
Conclusion
Without the efficient management of employee competence records, organizations can easily run into Quality issues by making false assumptions about employee competence. As George S. Patton Jr. said: “Success demands a high level of logistical and organizational competence.” A competent organization is an outcome of competent employees. Therefore, it is crucial to be mindful of your organization’s competence and to implement an eQMS solution that will help you drive a Smart Quality culture in your organization.