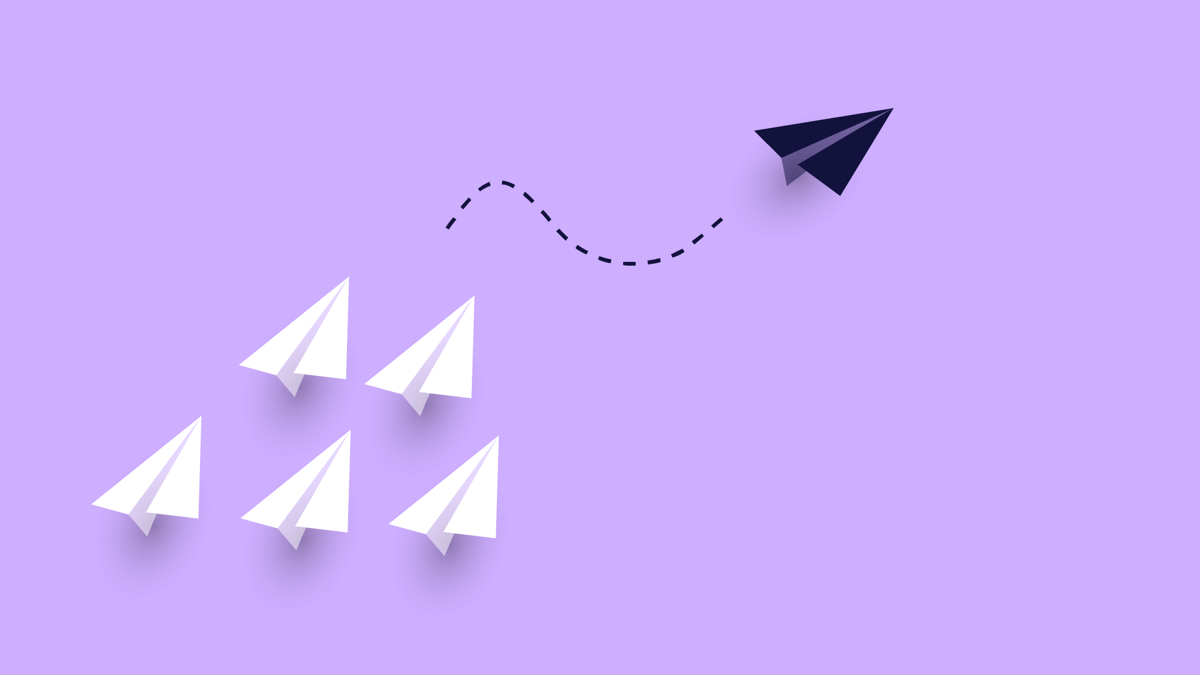
On October 20, 2022, I had the unique opportunity to attend Evgeniya Makarova‘s virtual talk at Scilife’s Smart Quality Summit.
I must admit: I was very excited to listen to her speech. I even bought brand-new white AirPods for the occasion! As a passionate advocate of the Smart Quality system, I just couldn’t miss the opportunity to hear her latest insights.
And Evgeniya didn’t disappoint at all. It was a great way to start the Scilife Summit for us all.
Evgeniya Makarova, Partner at McKinsey & Company, has unique and diverse expertise in Quality Compliance and Remediation. She specializes in transforming the operations of Life Sciences organizations into streamlined industry leaders. Her projects start with an initial status assessment for the organization across all areas. After the diagnosis, she implements a new operational strategy with specific plans to transform the Quality process into a Smart Quality system.
There were other great speakers at the Summit: Filip Heitbrink, CEO of Scilife; Sami Nas, Customer Success Manager at John Snow Labs; Mika Siitonen, Medical Development Manager at LabQuality; Lieve de Wolf, Quality Manager of CAR-T & Advanced Therapies at QBD Group; Robin Kerbel and Carlyn Whiting from Six Degrees Medical; and Jonathan Boel, Senior Project Manager at QBD. All of these experts showed us a new way of managing Quality with the right tools and systems. It is the start of a re-evolution of Quality:
Rethink, reconnect, re-imagine, and reinvent.
But first, let’s dive deeper into the main learnings from the McKinsey speech:
Differences between Traditional Quality and Smart Quality
On the one hand, it is no secret that traditional Quality is about delivering Quality at the lowest possible cost. Compliance and Quality are not considered valuable business drivers, but merely a cost of doing business. In the past, organizations assumed they had to bear this cost to avoid failures and deliver high-quality products.
On the other hand, we are now seeing a paradigm shift of what Quality can become. Smart Quality principles are built into Quality processes using different ways of working. Innovative and new technologies enable today’s organizations to act faster and produce higher-quality products and services at overall lower costs. The lesson here is that Quality can become a value driver throughout the value chain of an organization, from R&D to post-market.
As customer needs are constantly evolving, the 21st century organization needs to be proactive about collecting trend data from the market to adapt their internal processes to create value. The modern Life Sciences company also needs to unconditionally deliver on patient safety while meeting regulatory requirements.
The 5 Building Blocks of Smart Quality
McKinsey’s Evgeniya, talked about the Smart Quality approach as a combination of five building blocks that transform Quality processes in a new way that goes beyond compliance. Three of them are direct sources of value: Smart Quality Controls, Smart Quality Assurance, and Product and Process Mastery. The other two are enablers: Smart Quality Ways of Working, and Smart Compliance Foundation.
Let’s take a look at each building block:
1. Smart Quality Controls
Smart Quality Controls use digitized, automated, and integrated tools from the beginning of the value chain, from the development phase to the R&D. These tools identify the Critical Quality Attributes (CQAs) of the product and apply controls to the right Critical Control Points (CCP) of the process.
Smart Quality uses Design Thinking to redesign Quality processes with an end-user focus. Automation, digitalization, advanced analytics, artificial intelligence, and machine learning are novel tools that can streamline Quality processes. The use of paperless labs, documentation digitalization, and process automation controls at the shop floor can deliver up to a 50-100% increase in productivity, speed, and sustainability. That’s quite impressive, isn’t it?
How is Smart Quality managing out-of-specifications results (OOS) and deviations in Quality control labs? According to McKinsey, advanced analytics are key in the prevention and investigation of OOS. One of the bottlenecks of traditional labs is planning and scheduling. Advanced analytics remain essential to predicting the variability of sample arrivals and resource needs.
The most surprising fact for me is that McKinsey predicts traditional laboratories will disappear into shop floor real-time testing. In-line micro, water and air testing, in-process controls performed by the operators, and the use of pre-certified raw materials will speed up process lead times and reduce Quality costs.
So, parametric release will be the future. But how? Smart Quality will enable the release of products based on the evaluation of any information collected during the manufacturing process without performing the final control testing at the end of the manufacturing chain. It only makes sense if Life Sciences organizations seriously commit to digitizing and automating all processes. I am sure this is the future.
2. Smart Quality Assurance
The second block, Smart Quality Assurance uses optimized systems, automation, and artificial intelligence to completely redesign all traditional Quality processes, such as deviations, investigations, and complaints management. The new digital tools can be designed with user-friendly functionalities and gamification. This will motivate personnel to be accountable and integrate Quality principles into their day-to-day work more easily.
Does this improvement impact the customer somehow? Yes, absolutely. Quality integrated in the internal processes reduces the risk of failure, the time-to-market of new and improved products, and lowers the final cost to the consumer.
As I thought about this last statement, I imagined getting a Quality system right the first time with zero non-conformities. How is it possible?
3. Product and Process Mastery
According to McKinsey, this is due to the enabler of Product and Process Mastery. This third building block is focused on understanding all product parameters that are critical to product Quality. Advanced analytics again play a key role to predicting advance maintenance operations and Quality root-cause failures. Several McKinsey studies found a 30% improvement of yield in manufacturing. I mean, wow! That’s a significant cost reduction.
4. Smart Quality ways of working
Evgeniya said that the fourth block - Smart Quality ways of working - is a very important element as a supporting enabler of the key building blocks. This block includes collaboration initiatives that foster people’s capabilities to customize Quality processes in an effective way. Interdepartmental collaboration can add significant improvements to product R&D speed and efficiency.
5. Smart Quality compliance foundation
There is one last building block: Smart Quality compliance foundation. Although it is the final block, it is not any less important. Evgeniya stated that joining innovation with regulatory bodies allows them to go further in the design of the processes delivering the true intent of Quality systems. New products arrive on market faster because change approvals are easier. In other words, it is important to proactively engage regulators in a constructive dialogue and get their input if possible before implementing significant changes.
The Business Cases that Enlighten Smart Quality
After the initial theoretical explainer on the Smart Quality approach, we dove right into the best part of our McKinsey speech. I listened carefully to the next part with my eyes and ears wide open. Several examples enlightened me with the practical implementation of the Smart Quality approach: a digitized and automated paperless QC lab, an automated Quality complaint process and a digital Quality management review process.
The benefits you can obtain from this approach are impressive. The use of Smart Quality tools deliver efficiency, speed, and reduced waste. What I liked the most is the time savings that free up employees to devote their time to the important things.
How Gamification Improves Quality Culture
But what about Quality culture? As time passed, there was still no mention of this topic, until the moment arrived.
Evgeniya said that Quality culture is one of the hardest things to accomplish in a company. It is even more difficult than deploying technical solutions.
So, I wondered, what are the key issues that can motivate employees in a Smart Quality culture?
Evgeniya said the key is gamified training and platforms that motivate employees to use new Quality tools. Say what?! I love games!
In gamification, elements from games are used to make applications more enjoyable and engaging.
Make no mistake, employees won’t end up playing games at work. But gamification can address deviations, CAPAs, events, and training in an entertaining way. Interactive tools and new ways of learning are more effective than boring traditional training. Competition in learning becomes informative and exciting, mostly thanks to its interactivity.
Want to find out my 4 key takeaways from the summit?
Now you have learned about my impressions from the McKinsey speech at Scilife. Would you like to rewatch the full Smart Quality Summit?