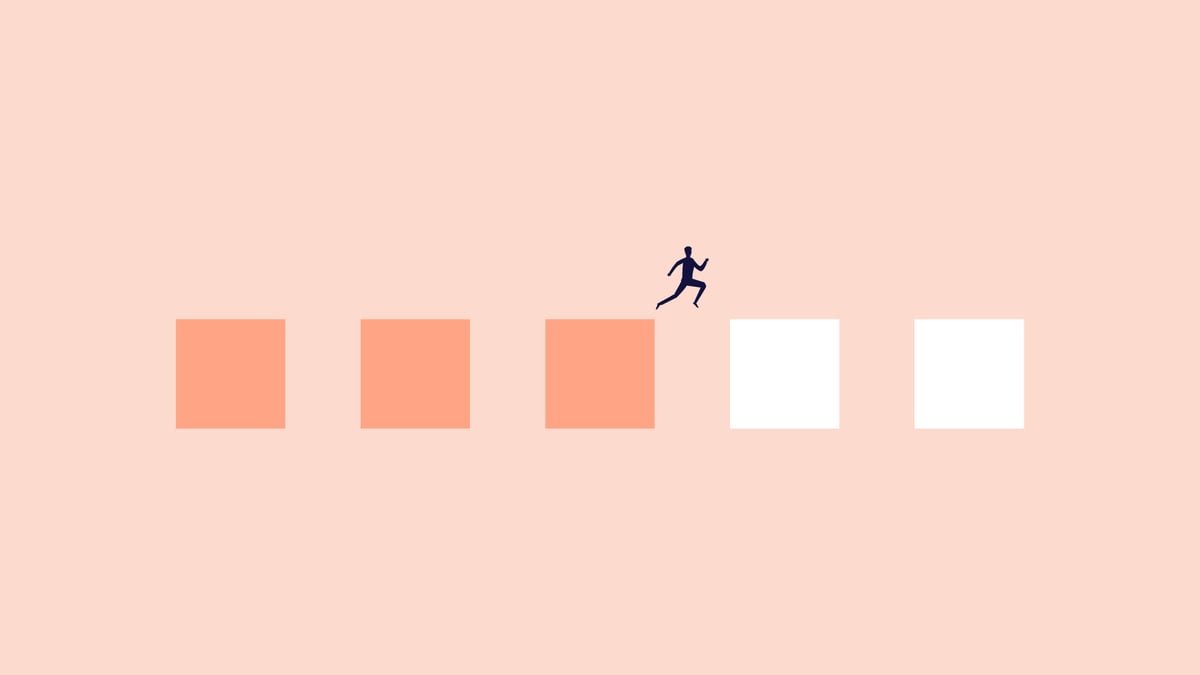
You’ve probably heard all kinds of advice and guidance for how to implement a Quality Management System. Some helpful. Some overwhelming.But the most effective guidance comes from real-world experience. As someone who’s worked hands-on with QMS implementation, I’m here to share a clear, proven approach that sets you up for lasting success.
In this article, I’ll show you how to implement a quality management system that works in practice, set clear goals, choose the right tool (such as an eQMS), and roll out your QMS without headaches. You’ll spend less time on paperwork and more time on the science you love.
Let’s get started.
Why is implementing a Quality Management System important?
Before we get into how to implement a quality management system, let’s understand why it's a strategic decision. It elevates operational performance and establishes a robust foundation for sustainable, long-term development. It is key for ensuring consistency in all your processes and, ultimately, guaranteeing your product quality and safety.
Think of a Quality Management System as your organization’s “NORTH star” for doing things the right way, every time.
Here’s why it really matters:
Navigate strategy
First, align all initiatives with your organization's vision. You must establish measurable, clear quality objectives that echo your customers’ deepest needs. This mapping ensures every initiative—from product design to customer support—steers you closer to satisfying your customers’ needs and improves trust.
Own processes
Next, claim ownership of every step. When you document and standardize your workflows, guesswork disappears. Your team knows exactly “how” to get things done, freeing everyone to focus on solving real problems rather than reinventing the wheel.
This consistency is your engine to operational excellence: reliable, repeatable, and ever-faster.
Review performance
Every great quality journey needs checkpoints. Schedule regular pit-stops—internal audits, KPIs, quality reviews, and customer feedback sessions—to measure how far you’ve come.
Reviewing your progress early can help you mitigate risks and avoid fixing later on. Think of it as star maps, so you can adjust your course before you fall off.
Take action
Insights without action are like starlight without direction. As soon as you spot a gap or opportunity, take a step forward. Implement a change, educate your team, or introduce a new tool that adapts to market changes.
Quick, tangible improvements build momentum and reinforce the message that quality isn’t theoretical, it’s something you live every day.
Harmonize culture
Finally, bring everyone onboard quality. Celebrate small victories, share lessons learned, and encourage open dialogue. When quality becomes a shared value rather than a box-ticking exercise, you create a self-sustaining culture where every team member feels empowered to contribute to your quality north-star goals.
Examples of Quality Management Systems and other methodologies
A modern Quality Management System isn’t “one size fits all” because every organization’s context, risks, objectives, and regulatory requirements differ.
Below is a concise overview of the most widely adopted frameworks and methodologies so you can see the spectrum of options. These examples of Quality Management Systems should help you choose to best direction to take for implementing your QMS.
What does a QMS require?
Now that you’ve seen examples of Quality Management Systems, it’s time we dive into the requirements to establish a practical QMS.
It usually falls into three layers: strategy, core requirements, and integration and sustainability.
Strategy
A credible QMS begins with intent. Leadership has to decide, in writing, that meeting customer needs and regulatory rules is a non-negotiable design feature of the business. From that decision flow, three strategic choices: process thinking, PDCA cycle, and risk-based thinking.
Start by shifting your mindset from isolated departments to process thinking. Map every activity you do —from initial design through delivery and post-market surveillance—and view each hand-off not as a nuisance, but as a risk you must actively manage.
- Use the Plan-Do-Check-Act (PDCA) cycle to drive controlled change. You set objectives and resources, execute the work, inspect the data, close the gaps, and then cycle back to planning. The loop never stops.
- Place risk-based thinking on top by identifying failures, deviations, or supplier issues while they are still inexpensive to fix, and place preventive controls into everyday tasks rather than fixing them later.
- This strategic layer links quality to profit by making failure prevention cheaper than failure correction. So, before even thinking about how to implement a quality management system, you should think about strategy first.
Core QMS requirements
Life-science firms operate under overlapping rulebooks: ISO 13485, ICH Q10, Good Manufacturing Practice, 21 CFR Part 11, and the FDA’s new Quality Management System Regulation (QMSR) that becomes compulsory on 2 February 2026.
Identifying the common spine makes alignment easier:
Context and scope
Define which sites, products, and software fall inside the QMS. Justify every exclusion in plain language.
Leadership and planning
Executives own the outcomes. They allocate people, budget, and infrastructure. They set measurable goals, and they review progress against risk.
Support architecture
Competent staff, validated equipment, secure data, and controlled documents keep the machine running. In the life sciences, that means software validation, equipment qualification, and data-integrity audits.
Operational control
From design and development, to QC, QA, supplier qualification, and audit management, each process needs documented criteria, acceptance limits, and evidence of execution.
Performance evaluation
Metrics and KPIs collect that matter: complaint trend, CAPA closure time, right-first-time batch rate, audit findings. Feed the numbers into management review so decisions ride on facts, not anecdotes.
Improvement
Every deviation triggers root-cause analysis. Corrective action is verified for effectiveness. Lessons are pushed to similar processes so the same mistake doesn't repeat itself.
Integration and sustainability
Quality has to sit in the same dashboards, budgets, and reviews as the rest of the business. If you park it in a silo, you will end up with paperwork nobody follows.
Here are three practices to close the loop:
- Quality objectives should be displayed in the same dashboard as revenue and R&D milestones. When the board reviews strategy, QMS data is on the first slide, not in the appendix.
- Records are your evidence. They prove compliance today and feed future risk models. Missing records put your company at regulatory risk.
- Performance is evaluated through data, and management reviews inform decision-making and reveal gaps.
As a final point, continuous improvement is non-negotiable. If your SOPs, templates, or training modules haven't changed in six months, assume they're outdated.
Documentation hierarchy as per the QMS standards
The first step in documenting your QMS involves deciding how to implement a quality management system structure that fits your business complexity.
Mostly, modern ISO standards split into two camps: the flexible and the prescriptive.
Knowing which camp your business falls into keeps you from over-engineering paperwork, or worse, leaving auditors guessing.
For instance, if you follow ISO 9001, you have the licence to design the hierarchy that best fits your operation, according to the complexity of your processes and the competence of your staff. This standard deliberately avoids forcing a “five-tier” pyramid of manuals, policies and objectives, procedures, work instructions, and records. Instead, it bundles everything under the banner of documented information.
In practice, you might keep four top-level documents—your quality policy and quality objectives, a set of processes, a list of cross-functional procedures, and records for your activities. ISO has no problem with that, as long as the system works.
In contrast, ISO 13485, which outlines requirements for QMS for medical devices, is more descriptive in its documentation requirements:
- Quality manual: It is a top-level document that includes the scope, makes reference to documented procedures, and outlines the structure of the documentation used in the QMS.
- Documented procedures: They are key documents of the QMS.
- Records: They are a special type of document and must be controlled to provide evidence of conformity to requirements and of the effective operation of the QMS.
- Other documentation: Quality policy and objectives, protocols, reports, plans, etc.
How to implement a Quality Management System
There are 5 steps to implementing a quality management system.
In the first step, you identify your internal and external business context.
In the second step, you plan what to do to deliver the product/service to the customer.
In the third step, the do stage, you implement your operations plan.
In the fourth step, the check stage, you assess the performance and identify which are the areas for improvement.
Lastly, in the fifth step, the act stage, you analyze the defects and apply changes and education.
Let’s see one by one each step:
Step 1: The context
At this early stage, understanding internal and external context helps shape your strategy for how to implement a quality management system aligned with your company’s direction. This includes consideration of factors that may affect your business, your goals, and your objectives need to be clearly defined at this stage.
1. External context
To understand your external context, you need to consider several factors:
- The uncertainties and economic changes
- The market needs
- Your competitors, suppliers, partners, and customers
- The regulatory bodies
- The changes in technology
- The social and cultural behaviors
- Changes in the political landscape
- Legal changes
- The economic environment
It is important to identify which are the interested parties who are affected by your work and understand their needs and expectations from you.
For example:
- According to ISO 9001, customers expect that an organization is able to consistently deliver products and services conforming to their requirements.
- According to medical devices, patients expect that medical devices are safe, and will improve their health and even save their lives.
- According to Pharmaceuticals, patients expect that every dose of medicine they take is safe and effective, free of contamination and defects.
2. Internal context
To understand your internal context, consider issues related to company values, quality culture, knowledge, and current performance.
Once you have identified the organization and its context, and the interested parties and their needs, it is time to determine the scope of the QMS.
A QMS can be established using the PDCA cycle and risk-based thinking aimed at taking advantage of opportunities and preventing undesirable results.
Step 2: Plan
1. Define your quality policy and quality processes
In this stage, the management with executive responsibility takes accountability for the effectiveness of the QMS, making it an essential part of how to implement a quality management system with purpose and clarity. The management demonstrates leadership and commitment by establishing quality intentions and directions to ensure they are understood by the whole company.
It is necessary to receive feedback from employees to succeed. This is the quality policy supported by the strategic direction.
A quality policy defines the quality practices, resources, responsibilities, and activities that are relevant to the business. It also shows how the requirements for quality will be met according to the strategic direction.
Define clearly the quality of your product or service: specification limits and compliance requirements.
2. Strategic and tactical level: Define your business goals, objectives, and metrics
At this level, you refer to the plans and actions that your company is taking to achieve the vision and goals for the future according to the strategy.
Management defines the business goals, specific objectives, and metrics that will help to evaluate the performance.
It is important to define:
- What will be done
- What resources are needed
- Who is responsible for each process, task, etc
- When will it be completed
- How will the results be evaluated
Quality objectives should be aligned with the business goals and regulations.
The resources needed for the establishment, implementation, maintenance, and continual improvement of a quality management system of quality are:
- People
- Infrastructure
- Process environment
- Monitoring and measurements
- Organizational knowledge
3. Operational level: Determine and map your processes
At this level, you need to map your processes, identifying the inputs and outputs, and the correlation and interaction between the processes.
A good way to do so is to document all the flows of the processes to assure they will be followed as defined.
It is time to apply risk management principles to identify the risks. Plan actions to address the risks by eliminating, preventing, or reducing the likelihood of happening.
What is a risk?
According to ISO 9001:2015: “Risk is the effect of uncertainty on an unexpected result”
- What could happen
- How likely is it to happen
- What effect would it have if it happened
Do also consider addressing opportunities. The new technology, digitalization, new practices, and quality culture can leverage the potential to gain competitiveness.
4. Determine your resources
Personnel
Map out your organizational structure and the key responsibilities of employees in every function. This will enable employees to understand what their key deliverables are in terms of quality, and how they can collaborate with employees in other functions.
Infrastructure and materials
The organization shall determine, provide, and maintain the infrastructure and environment that is necessary for the operation of its processes and to achieve conformity of products and services.
Provide adequate facilities, environment, equipment, technology, tools, materials, hardware, and software that are needed for your operations to obtain your product and services.
5. Define your quality system documentation: procedures, instructions, and records
Good documentation is key to operating in compliance with quality system needs and regulatory requirements. The objective is to establish, control, monitor, and record all activities which directly or indirectly impact all aspects of the quality of the products and services.
Standard Operating Procedures, work instructions, and methods are used to give direction and indications, while records and reports are the proof that the processes have been done and give assurance of traceability.
Step 3: Do (Operations)
“Quality doesn’t happen by chance. Quality happens by design.”
This is where theory becomes practice. How to implement a quality management system also means ensuring execution follows design, and quality is built into the product.
In this stage, you execute your plans (what, who, when, how) for manufacturing activities. Use a system to monitor process performance, inspection, and testing activities, to verify that products and materials conform to specified requirements.
One of the ways of building the desired quality into the product is to ensure that the natural variation in the product is as low as possible and smaller than the defined quality specification. Control this variation.
This is to ensure that the desired quality of the product will be manufactured consistently and repeatedly, batch after batch.
Step 4: Check. Monitor quality, analyze, and review your process performance
"Without data, you’re just another person with an opinion."
W. Edwards Deming
To ensure that a state of control is maintained and facilitates continual improvement, plan to monitor process performance and product quality, as well as the effectiveness of the quality management system.
By monitoring processes and controls, it should be possible to identify areas of continual improvement and ensure that products are manufactured according to desired quality.
The degree of customer satisfaction shall be monitored to determine their needs and expectations. You can use surveys, meetings, feedback, etc.
You should analyze and evaluate the following data:
- The conformity of products and services
- If nonconformances have been addressed
- The degree of customer satisfaction
- The performance of external suppliers
- If the actions to address risks have been effective
- The QMS performance
Retain appropriate documented information from monitoring as evidence of fitness for purpose.
1. Corrective action and preventive action (CAPA) system
Whenever there are complaints, product rejections, non-conformances, recalls, deviations, audit and regulatory inspections with findings, and trends from process performance and product quality monitoring, investigations should be done to find the root cause. The application of a CAPA methodology should result in product and process improvements and enhanced product and process understanding.
2. Change management system
Any change to be applied in any process, because of a CAPA, continual improvement, innovation, etc, needs to be evaluated and approved before implementation. Changes must be done in a planned and systematic manner.
A change management system needs to be in place to ensure that the change is undertaken in a timely and effective manner without unintended consequences.
3. Management review of process performance and product quality
The management review helps to assure process performance and product quality are managed. It is useful to identify appropriate actions for improvement, training, operational changes, etc.
4. Periodic quality reviews:
Periodic quality reviews ensure a QMS is continuing to be suitable, adequate, and effective. It covers complaints, recalls, KPIs and metrics, customer satisfaction, etc.
5. Quality audits
It covers the results of self-audits, regulatory inspections and findings, external audits and other assessments, and commitments made to regulatory authorities.
Internal audits shall be conducted at planned intervals to provide information about the conformity of each process to the QMS requirements and regulations.
Step 5: Act. Define your defects and take action to improve
1. Identify your defects and areas for improvement
This step is the most important part of the PDCA cycle of a Quality Management System. It is about taking actions to improve performance.
Its primary purpose is to respond to the insights gained from the "Check" phase (monitoring, measurement, analysis, and evaluation)
- Address non-conformities and deviations
- Focus on root-cause investigations
- Apply CAPAs
- Use lessons learned
- Anticipate and react to risks and opportunities
- Enhance drive for innovation
Without actions for improvement, the efforts and activities applied throughout the system will be fruitless.
The actions for improvement drive your system to be better. Use nonconformities as an opportunity for improvement.
This ensures that the organization learns from its experiences, addresses identified issues, capitalizes on opportunities, and consequently enhances its overall performance and the effectiveness of its quality management system.
It potentially engages your customer, reduces error, and saves money.
This is why we continually need to do things smarter and better.
The ways to be effective can be summarized in 4 ways:
- Being reactive to non-conformities
- Being gradual, looking for incremental improvements
- Being creative, using innovation to drive improvement
- Being transformational, implementing big changes, such as digitalization
2. Define organization knowledge and training
Determine what knowledge is necessary for the operations and processes functioning. Document the knowledge of procedures and work instructions in a clear and understandable way without additional fluff.
Share the knowledge with employees and plan a learning path to upgrade people’s skills according to business objectives and plans. Give appropriate education and training to ensure that people are competent in their work. Evaluate the effectiveness of training plans and apply actions if needed.
Ways to implement your QMS: Implementing a digital quality management system
A QMS can be established and maintained through various approaches, primarily categorized as paper-based, hybrid, or digital systems.
Paper-based Quality Management System
The traditional paper-based approach relies heavily on physical documents and manual records for all QMS processes. This includes quality manuals, procedures, work instructions, forms, and records, all maintained in hard copy.
For instance, records of complaints and responses would be physically recorded and stored in folders and cabinets. While simple to initiate without significant technological investment, managing updates, distribution, and retrieval of documents can be labor-intensive.
Ensuring that only current versions are in use and preventing the unintended use of obsolete documents requires strict control procedures.
Hybrid Quality Management System
Hybrid approach combines elements of both paper-based and digital systems. An organization might use electronic means for communication and certain data management, while still retaining physical documents for other critical records or processes.
For example, some companies issue reports as hard copies or by electronic means, and some data is managed through non-computerized systems alongside computer systems.
This mixed approach offers some flexibility but can introduce complexities in maintaining consistency, traceability, and ensuring all relevant information is readily accessible across different formats.
Managing electronic files and magnetic recording media alongside paper records also requires careful attention to prevent "loss as a result of mishandling or obsolescence.
Digital Quality Management System (eQMS)
I will never forget the day I opened a dusty binder stuffed with 24 versions of the same SOP, each stamped and initialed by people who’d left the company, while the auditor tapped their pen, impatiently waiting.
As a QC/QA Compliance officer in a European pharma lab, I spent more time hunting for the latest document than doing real work. With ever-changing rules like EU GMP, EU MDR, IVDR, and ISO updates, it felt like there was no end to the paperwork pressure.
Now, imagine every procedure, issue report and training record stored online, easy to find, always up to date, and ready for any audit.
That’s what a digital quality management system does.
A well-established digital quality management system will allow you to meet both customer and organizational requirements, easing the task of becoming fully compliant and generating confidence with the customers, empowering improvement and growth.
Also, it’ll help you prevent any possible mistakes and, consequently, lower costs and waste, identify training opportunities, and set a common direction for the whole organization.
How, you may ask?
A digital quality management system leverages computer software and information systems to manage all aspects of the QMS electronically. This includes digital documentation, electronic record-keeping, automated workflows, and integrated data analysis tools. An eQMS can also facilitate the collection and analysis of data for continual review and analysis, and identifying trends and shifts.
If you're exploring how to implement a quality management system using digital tools, an eQMS can give you speed, traceability, and compliance from day one.
Best practices for implementing a quality management system
When you look at how to implement a quality management system, best practices such as clear documentation, risk-based thinking, and strong data integrity play a vital role. It’s about building a system that genuinely supports product quality and patient safety.
Here are some key practices that can make a real difference:
Set clear documentation standards
Define what documents you need, how they’re created, stored, and managed—regardless of whether you’re using paper, hybrid solutions, or a fully digital eQMS.
If you are using an eQMS, make sure it’s properly validated and has controls in place to protect data integrity.
Use a clear hierarchy for your documentation: policies at the top, followed by processes, procedures, and records. Assign governance roles—someone needs to own templates, master documents, and the rules for creating official copies and managing records.
Align with clear objectives and controls
Your QMS should help you manage everything that affects the quality and safety of your product, both directly and indirectly. Set clear, risk-based objectives, and ensure your system supports traceable, complete, and accurate documentation throughout its lifecycle.
Take a risk-based approach
Use risk management throughout the document and data lifecycle. Not everything needs the same level of control, but you do need to justify why you treat some things differently.
The depth of data governance and risk management activities should be justified and commensurate with the risks to product quality and patient safety. Decisions on data integrity measures should be based on documented rationale and risk assessment.
Protect Data Integrity (ALCOA++)
The basics still apply, whether you’re working with paper or digital systems: data should be Attributable, Legible, Contemporaneous, Original, Accurate, Complete, Consistent, Enduring, Available, and Traceable.
That means:
- Instructions are clear, signed by authorized people, and uniquely identified.
- Every revision is documented and tracked.
- Entries are permanent. No white-out, no disappearing ink.
- Records are completed when actions are taken. Not later.
- If you outsource documentation, the same rules apply.
- Any alteration to an entry on a document should be signed and dated, permit reading of the original information, and, where appropriate, include the reason for the alteration.
Control document lifecycle
Whether it's a procedure, work instruction, or any other type, every document should be created, reviewed, approved, and updated in a controlled way. That includes managing master templates, ensuring users have the current version, and preventing outdated documents from reappearing at the worst possible time.
Retain records securely
Think long-term. Make sure records stay legible and complete throughout their required retention period. That includes having backup, restoration, and archiving procedures, especially for electronic records.
And remember: records must be available for review at any time in a human-readable format.
Key takeaways
- Build quality into your foundations. Implementing a QMS is about embedding quality into your processes from the ground up. It ensures every team, from R&D to operations, speaks the same language when it comes to product safety, compliance, and customer satisfaction.
- Keep it simple. Use a practical hierarchy: policies, procedures, work instructions, and records. Whether you’re using paper, hybrid, or digital systems, what matters most is that your documentation is accurate, up to date, and accessible when needed.
- An electronic QMS gives you a head start. Starting with an eQMS means no legacy paper trails to migrate later. You save time, reduce errors, and streamline audits. Validation, traceability, and version control are built-in, helping you scale quality from day one.
Conclusion
Learning how to implement a quality management system effectively is what transforms compliance into confidence.
It doesn’t have to feel like a mountain of paperwork or a regulatory maze. Done right, your QMS becomes a powerful tool, not just for passing audits, but for building safer products, reducing waste, and fostering a quality-driven culture.
And if you’re starting fresh, going digital from the beginning is often the smartest move. At Scilife, we’ve designed our digital quality management system to simplify the heavy lifting, so you can focus on continuous improvement, not document chasing.
Because in the end, quality isn’t just about compliance, it’s about confidence. In your processes, your product, and your people.